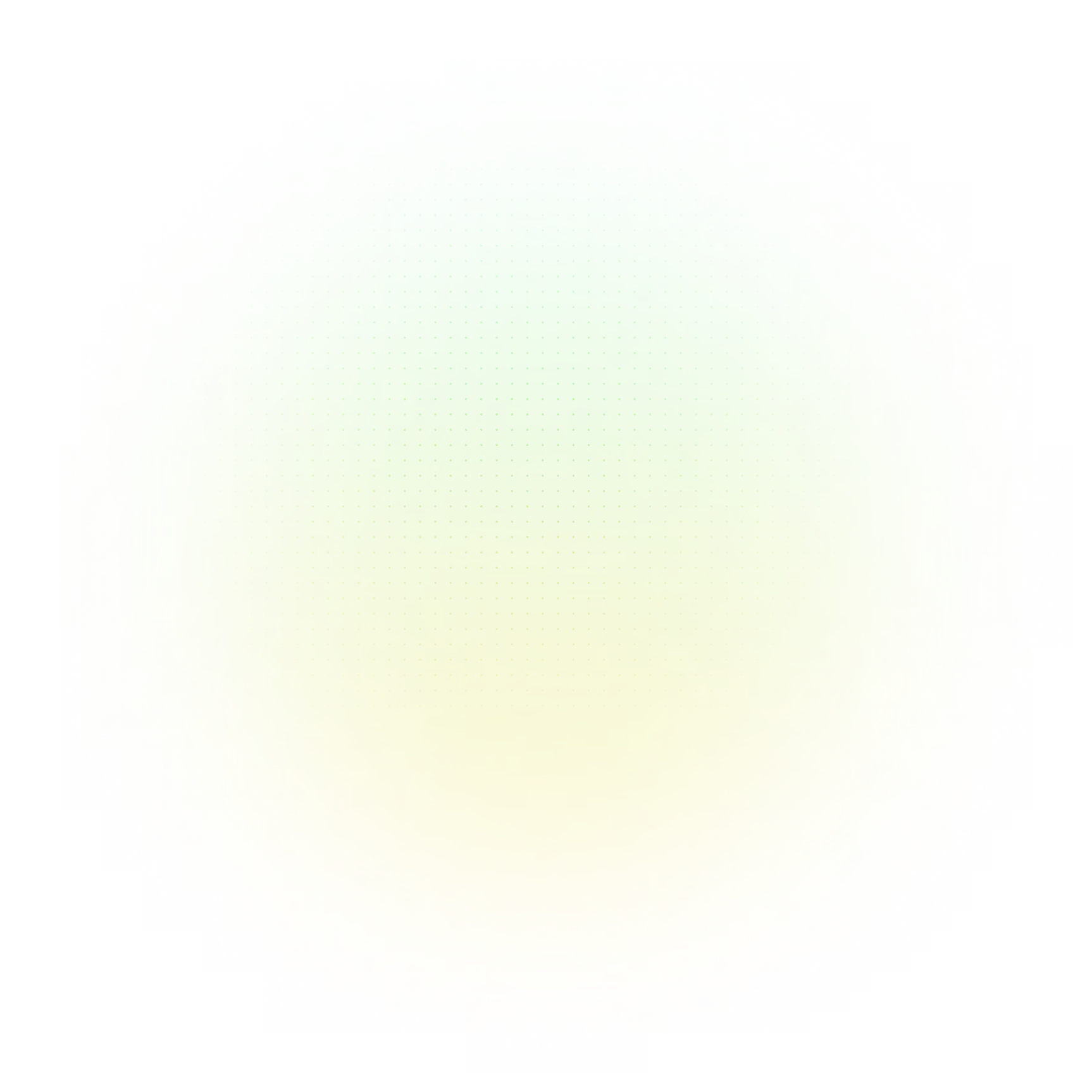
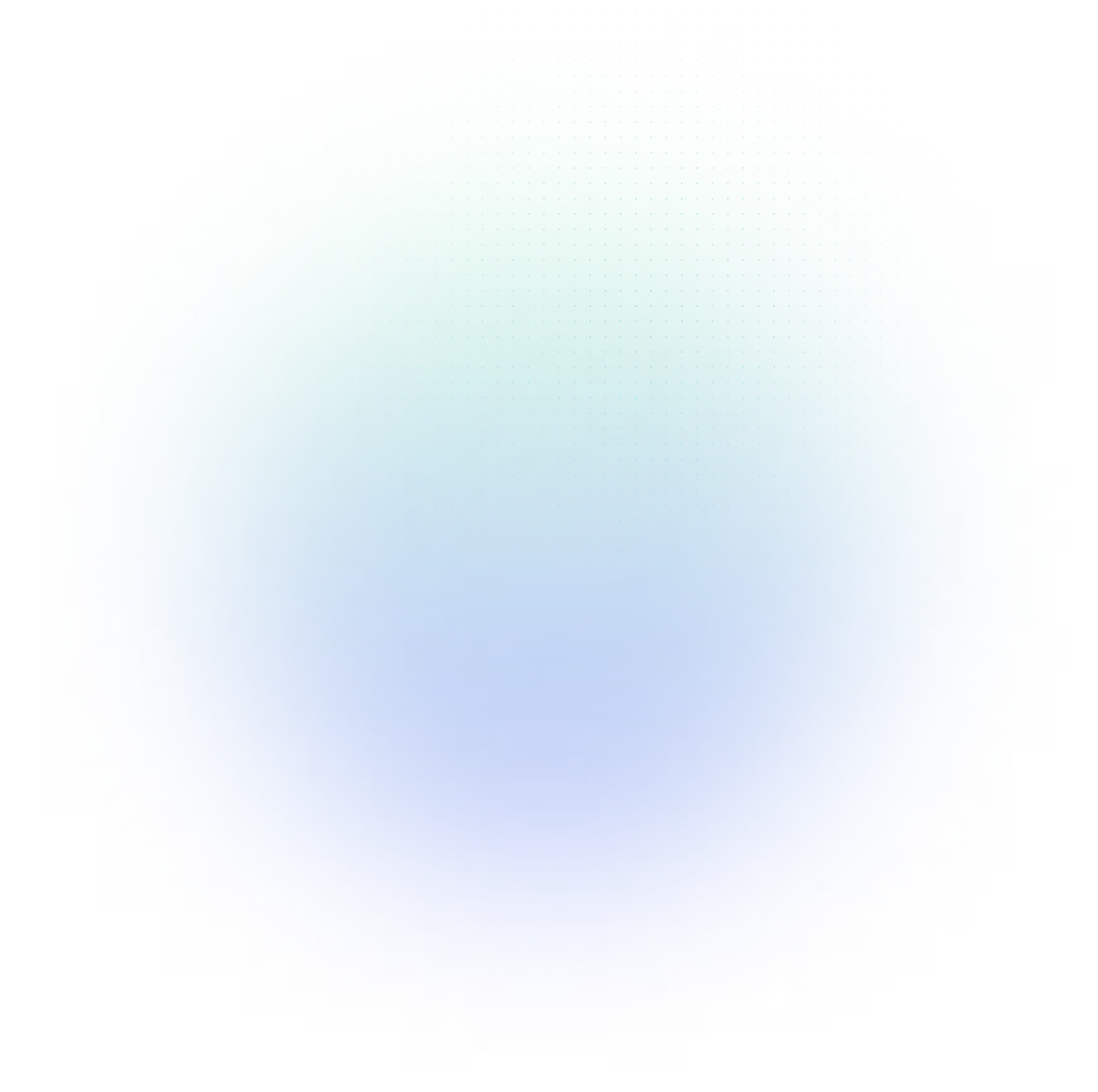
In today’s rapidly evolving business landscape, the ability to effectively pinpoint and resolve the root causes of issues is crucial for sustaining operational effectiveness and ensuring long-term growth. Root Cause Analysis (RCA) is a methodical approach that enables organizations to discover the fundamental issues behind a problem, facilitating the implementation of impactful solutions rather than focusing on symptoms. There are numerous techniques within RCA, each tailored to different challenges and environments. In this blog post, we will delve into the various types of root cause analysis, when to apply each technique, and how they can improve your problem-solving skills.
What is Root Cause Analysis?
Root Cause Analysis (RCA) is a systematic problem-solving method aimed at uncovering the underlying causes of issues rather than just addressing their symptoms. Imagine trying to fix a leaky faucet by only mopping up the water instead of repairing the source of the leak. RCA allows organizations to dig deeper, identifying and resolving the core problems that lead to frustrations and inefficiencies.
This powerful approach is widely used across various sectors, including manufacturing, oil and gas, mining, paper and forest products, healthcare, information technology, and service industries. By implementing RCA, companies can optimize processes, improve quality, and significantly reduce the risk of recurring issues.
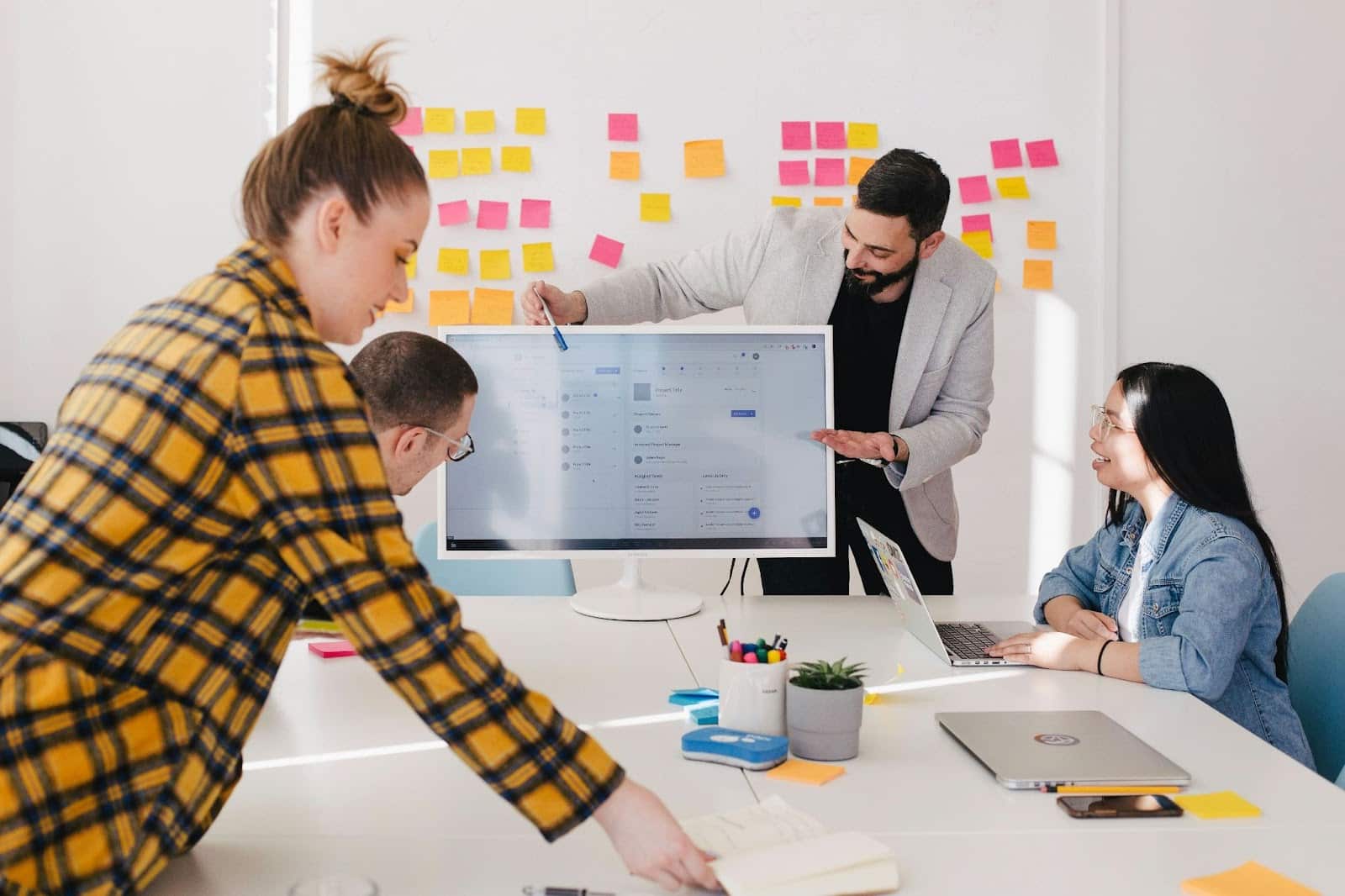
Types of Root Cause Analysis Methods
1. The 5 Whys Technique
The 5 Whys technique involves asking “why” repeatedly—typically five times—to delve deeper into the cause of a problem. By continuing to ask why for each answer, teams can uncover the root cause. This method is ideal for straightforward problems where the cause-and-effect relationship is clear.
For example, in a manufacturing facility, if a machine fails, asking why it failed might lead to:
- The machine had overheated.
- Why did it overheat? The cooling system failed.
- Why did the cooling system fail? It wasn’t maintained.
This simple yet effective technique is best suited for small to medium-sized issues or when the problem involves limited complexity.
2. Fishbone Diagram (Ishikawa Diagram)
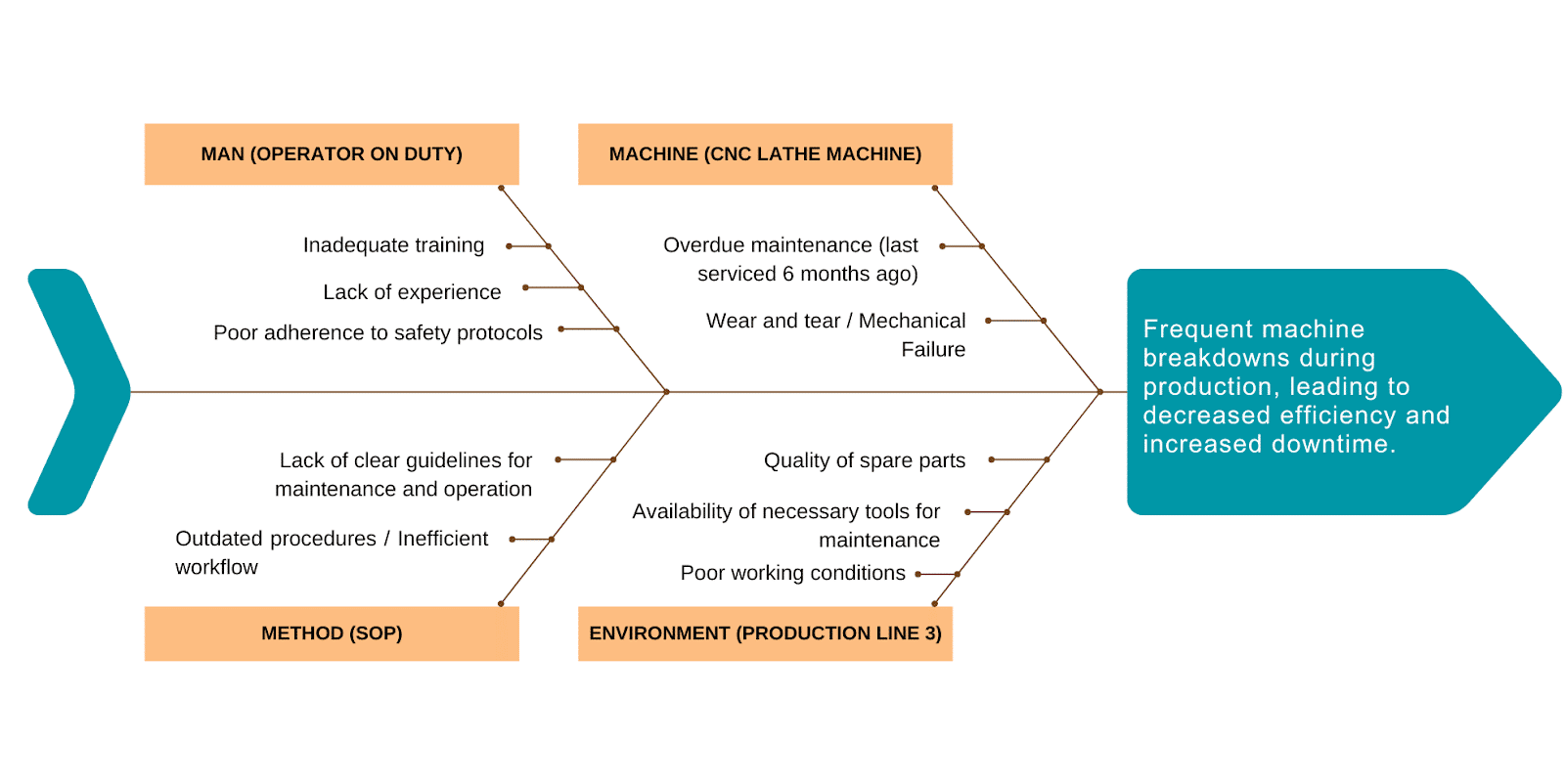
The fishbone diagram visually organizes potential causes of a problem in a structured format. It resembles a fish skeleton, with the main problem at the head and the contributing factors as bones branching off. This method is best for complex problems with multiple potential causes that may involve various factors, such as people, processes, materials, and equipment.
For example, if a product consistently fails quality tests, a fishbone diagram can help identify causes across categories such as:
- People: Lack of training.
- Process: Inefficient workflows.
- Materials: Low-quality raw materials.
This method is particularly useful in brainstorming sessions with cross-functional teams to capture diverse perspectives.
3. Fault Tree Analysis (FTA)
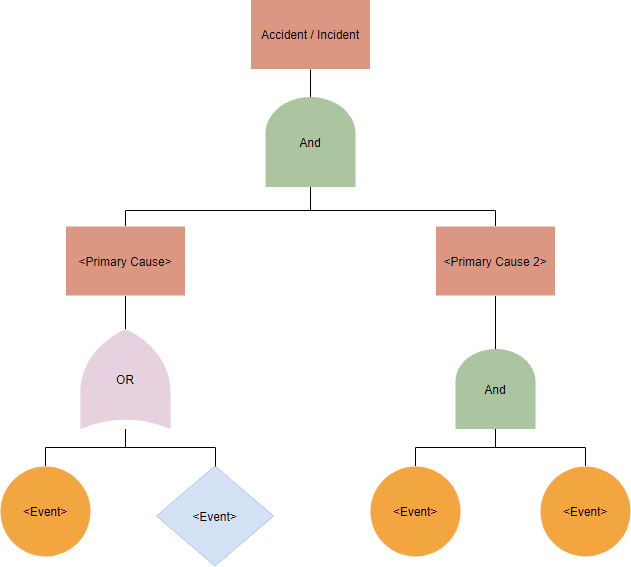
Fault Tree Analysis uses a top-down approach to identify the root causes of a system failure. It begins with the undesirable event and breaks it down into its causes using logical symbols and diagrams. FTA is suitable for complex systems where failures can result from multiple contributing factors. It’s particularly valuable in industries like aerospace, nuclear power, and healthcare.
For example, in a healthcare setting, if a patient experiences a medication error, an FTA can help trace the issue back through various levels of potential causes, such as
- Prescription errors
- Dispensing errors
- Administration errors
This method provides a comprehensive view of the interrelated factors leading to a failure.
4. Pareto Analysis
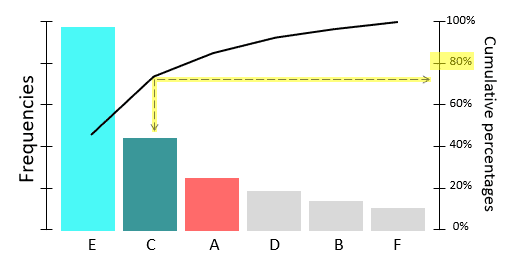
The Pareto Principle, or the 80/20 rule, suggests that 80% of problems often arise from 20% of the causes. This method involves identifying the most significant issues and focusing efforts on resolving them. Use Pareto analysis when you have multiple problems and want to prioritize which issues to address based on their impact.
For example, in a manufacturing plant experiencing numerous defects, a Pareto analysis might reveal that a small number of defects are responsible for the majority of quality issues. By addressing these key defect types, organizations can significantly reduce overall defects.
5. Scatter Diagrams
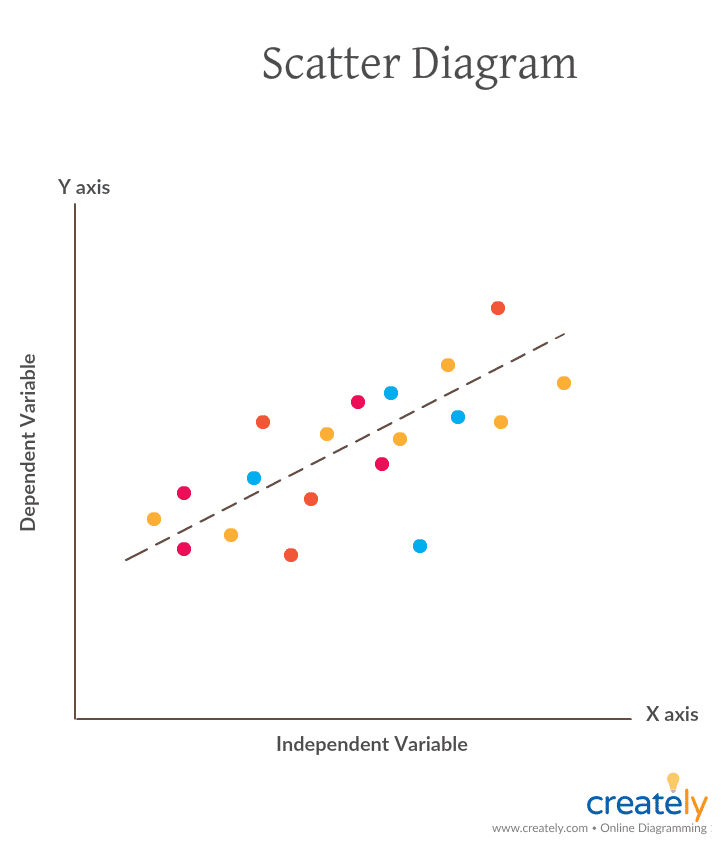
This graphical method plots data points on a Cartesian plane, allowing teams to visualize correlations between variables. Scatter diagrams help identify relationships between two variables and assess how one variable may affect another.
For example, a restaurant might use a scatter diagram to analyze the relationship between wait times and customer satisfaction scores. If a pattern emerges showing that longer wait times lead to lower satisfaction, the restaurant can focus on reducing wait times to improve overall customer experiences.
Conclusion
Understanding the various types of Root Cause Analysis (RCA) methods and knowing when to use each one is crucial for effective problem-solving in any organization. Choosing the right RCA technique for your specific situation allows you to dig deeper into the underlying issues and develop actionable solutions that prevent future problems.
Think of it this way: just as a doctor diagnoses an illness by considering different symptoms, you can tackle organizational challenges by applying the appropriate RCA method. From the straightforward approach of the 5 Whys technique to the more detailed Fishbone Diagrams and Fault Tree Analysis, each method has unique strengths and ideal applications.
By incorporating these techniques into your problem-solving processes, you empower your organization to face challenges head-on. Not only will this drive continuous improvement, but it will also foster a culture of collaboration and learning. As you tackle problems together, you build a stronger, more resilient team ready to overcome any obstacle.
So, take the time to explore these RCA methods and watch how they transform your approach to problem-solving, turning challenges into opportunities for growth and success.
Key Takeaways
- 5 Whys Technique: Best for straightforward problems; quick and easy to implement.
- Fishbone Diagram: Ideal for complex issues with multiple potential causes.
- Fault Tree Analysis: Suitable for intricate systems where the cost of a problem is particularly high.
- Pareto Analysis: Helps prioritize issues based on impact; focuses efforts on the most significant problems.
- Scatter Diagrams: Useful for analyzing relationships between variables.
By utilizing these RCA methods effectively, organizations can improve their operations and reduce the likelihood of recurring problems, leading to long-term success.
Ignite your curiosity, subscribe now!
Stay informed and connected with the latest updates by subscribing today!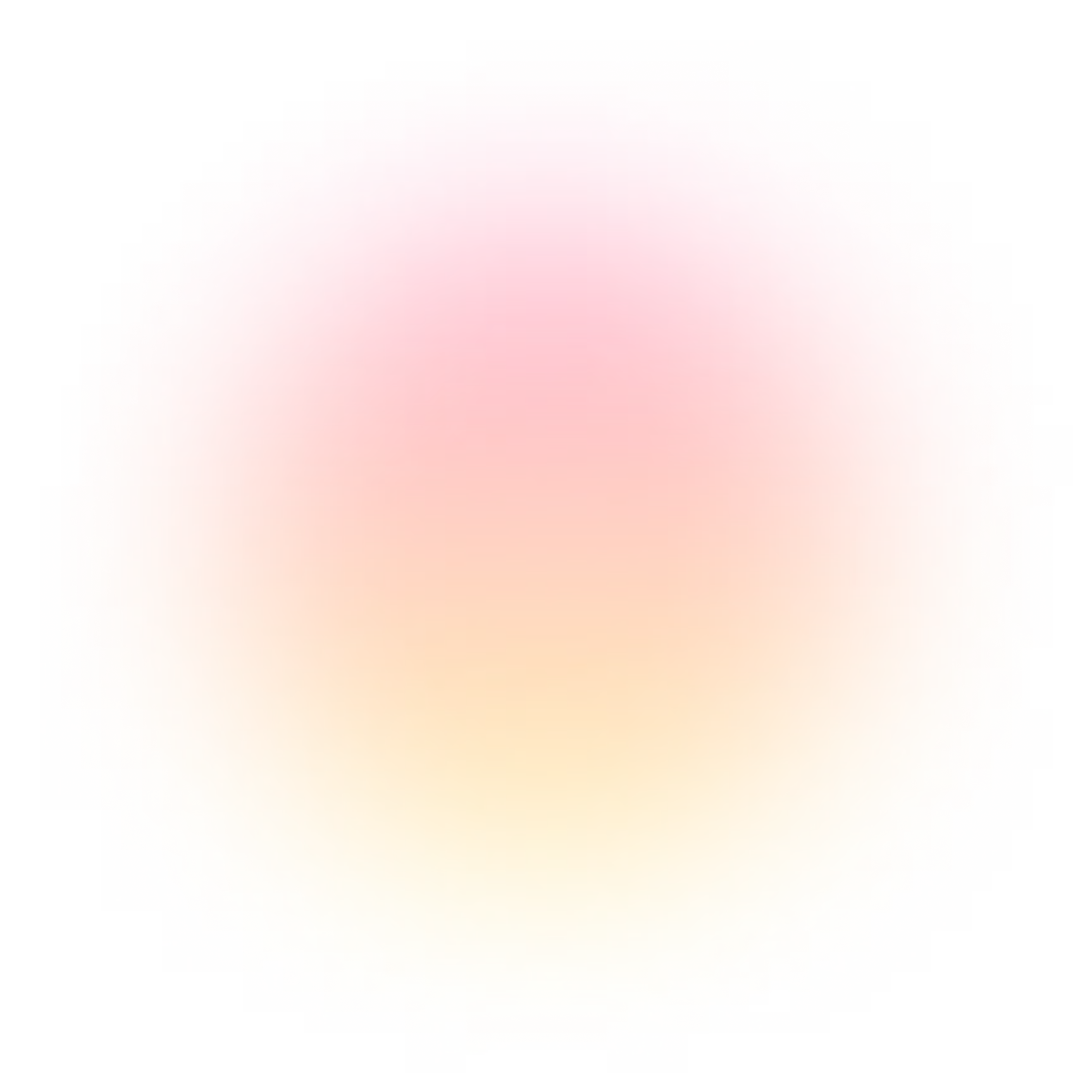
Recent Comments