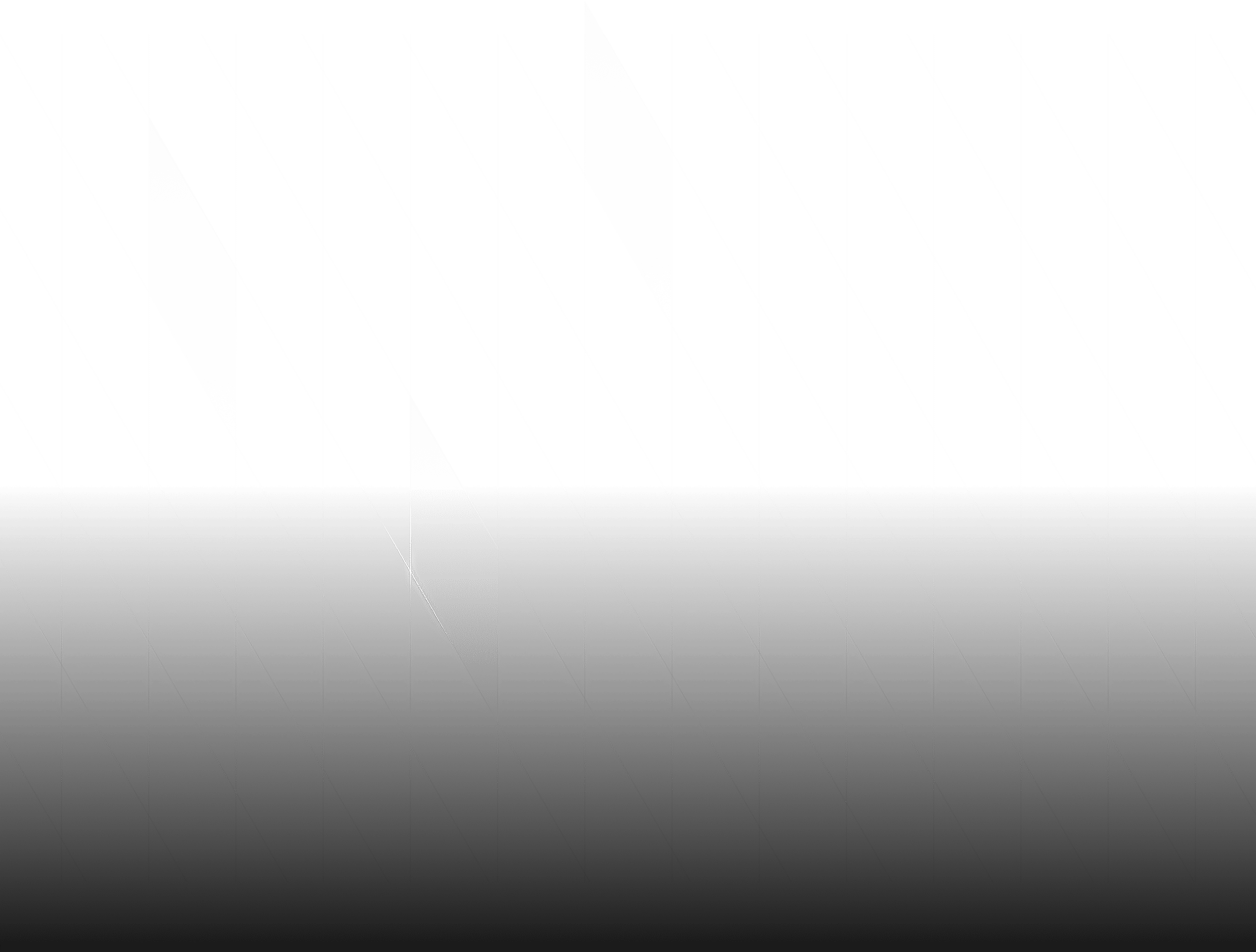
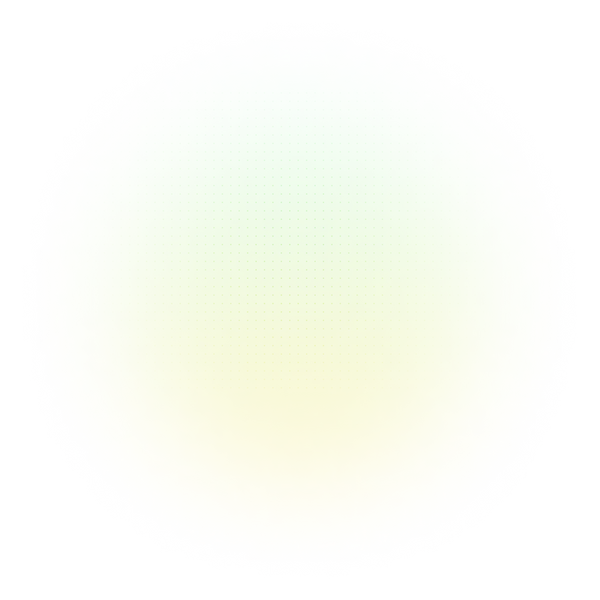

At Reliability, we’re on a mission to help enhance strategic decision-making and operational excellence through the power of Root Cause Analysis, and I hope this article will be helpful!
Our goal is to help you better understand root cause analysis by offering insights and practical tips based on years of experience. Whether you’re new to doing RCAs or a seasoned pro, we trust this will be useful in your journey towards working hard and working smart.
———————
In the bustling facility of Aberdeen 123, located in the heart of Site 3, Department 7, the hum of machinery signifies productivity and progress.
Yet, on an otherwise routine day, a persistent and chronic pump failure on pump CP-002 brought operations to a screeching halt, costing the facility a staggering $180,000.
This case study dives deep into the incident, unraveling the disruption caused, and how the power of Root Cause Analysis (RCA) with PROACT® methodology helped correct and move to the next level of reliability.
The Incident
It was the 19th of June, 2023, at precisely 23:17 when the inevitable happened. Pump CP-002, a critical component in the facility’s operations, failed unexpectedly. The shutdown caused significant downtime and disrupted the workflow, leading to considerable financial losses. The immediate question on everyone’s mind was, “Why did this happen?”
Disruption
For the product manager, the failure was a nightmare. The facility was already running a tight schedule, and any downtime meant a domino effect of delays. Employees, who were used to the rhythmic pulse of the pumps, were now dealing with the unsettling silence and the pressure of getting the system back online.
The Aberdeen 123 site has always prided itself on its efficiency and reliability. However, this chronic failure was a blow to their reputation. It wasn’t just about the immediate financial cost; it was about the trust and reliability the facility was known for. The key team members were thrust into the forefront of addressing this crisis. The urgency was palpable; every passing minute translated to mounting losses and increasing frustration.
Amidst the chaos, the facility turned to the PROACT® Root Cause Analysis (RCA) methodology. This systematic approach promised not just a fix but a thorough understanding of the problem to prevent future occurrences.
Initial Findings
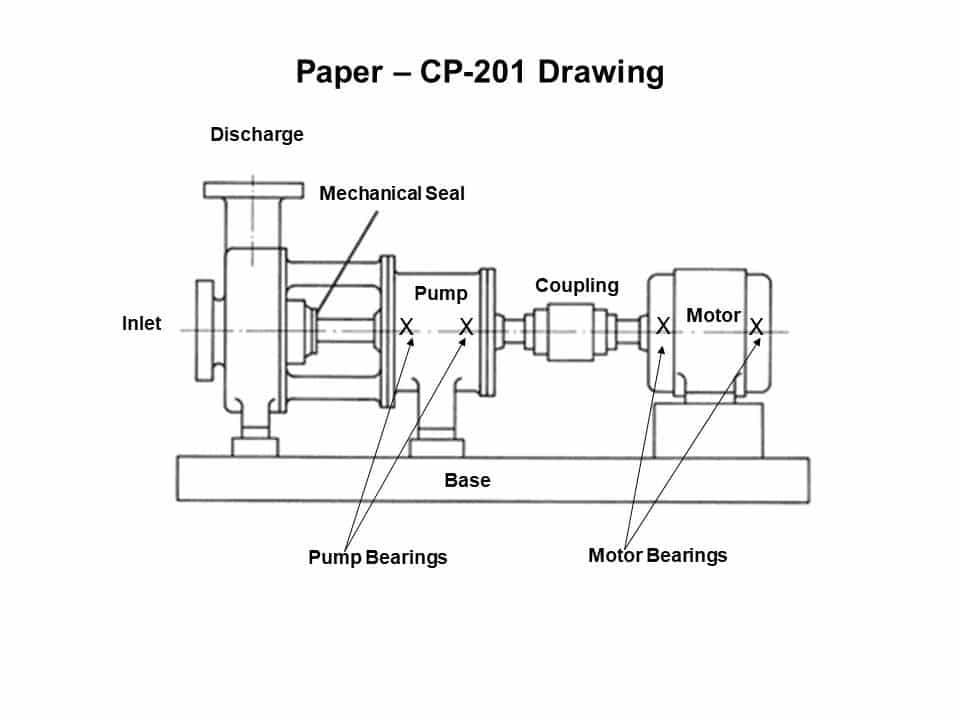
The investigation began promptly on June 20, 2023. The team, leveraging the PROACT® methodology, embarked on a journey to peel back the layers of the issue. The first finding was the improper installation of the pump. Further probing revealed that the misalignment was not just a one-off mistake but a symptom of deeper systemic issues.
Detailed Analysis
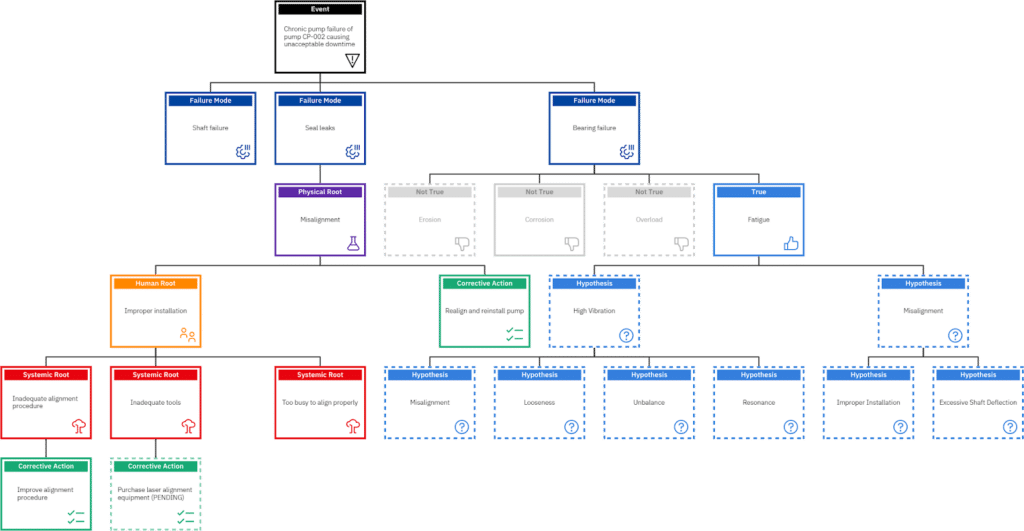
Once the team got together, they sought to break apart the possible causes and came up with these four analyses:
- Improper Installation: It was discovered that the pump wasn’t aligned properly during installation. The rush to get the pump operational led to oversight and shortcuts.
- Inadequate Tools: The team was lacking proper tools for precise alignment. The absence of laser alignment equipment was a critical gap.
- Misalignment: Continuous operations with a misaligned pump exacerbated wear and tear, leading to the failure.
- Inadequate Alignment Procedure: The existing procedures for pump alignment were found lacking detail and rigor, contributing to repeated misalignment.
The human element was significant. The team was under immense pressure, often too busy to follow the proper alignment protocols meticulously. This highlighted a systemic issue: needing adequate tools and a robust alignment procedure.
Corrective Actions
The RCA team, guided by the PROACT® framework, formulated a comprehensive plan to address these root causes.
- Purchase Laser Alignment Equipment: This was a pending action, critical for ensuring precise alignment in future installations.
- Realign and Reinstall Pump: The immediate step was to correctly align and reinstall the pump, following the improved procedures.
- Improve Alignment Procedure: The procedure was revamped to include detailed steps and checks, ensuring no shortcuts could be taken.
Implementation and Results
By February 10, 2024, the analysis was completed, and corrective actions were well underway. The facility not only rectified the immediate issue but also fortified its processes against future failures.
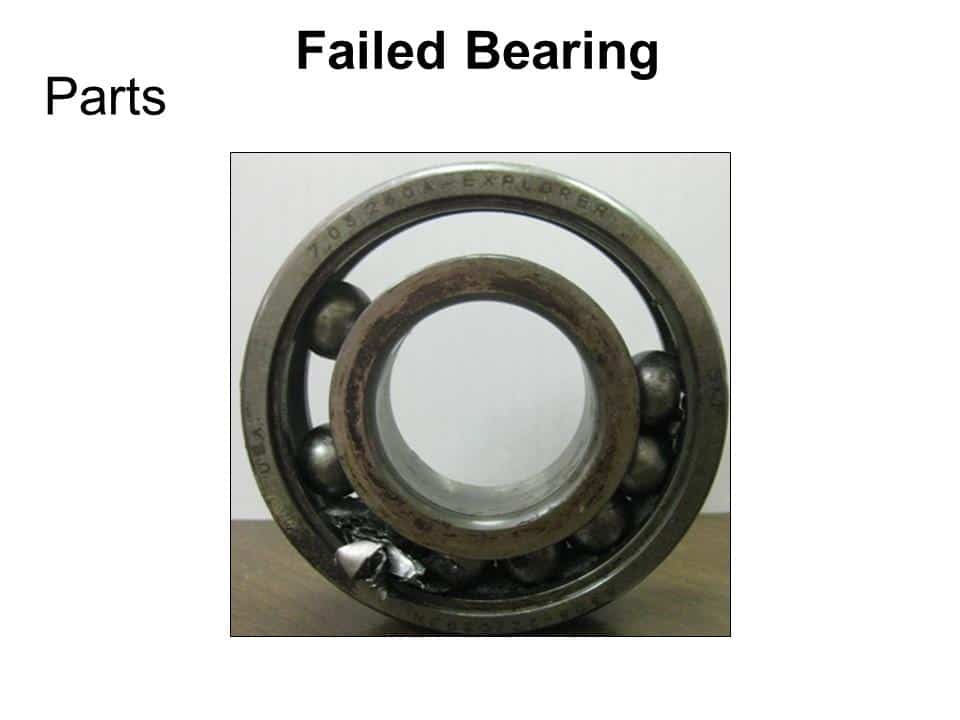
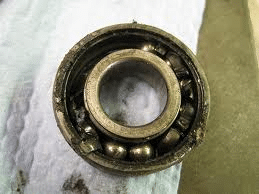
Above: Failed Bearing Parts
Visual inspections conducted by the team members for erosion and corrosion ensured no further vulnerabilities existed. The inspections confirmed the integrity of the bearings, ruling out additional physical damage. The facility invested in training programs for its staff, emphasizing the importance of proper installation and alignment procedures. Using laser alignment tools became standard practice, significantly reducing the risk of misalignment.
Proactive Measures for Future Reliability
The incident at Aberdeen 123 served as a wake-up call. The facility adopted a proactive approach to maintenance and reliability, integrating continuous improvement into its operations. The PROACT® methodology became a cornerstone of their reliability program, ensuring that every failure was not just a setback but an opportunity to enhance their processes.
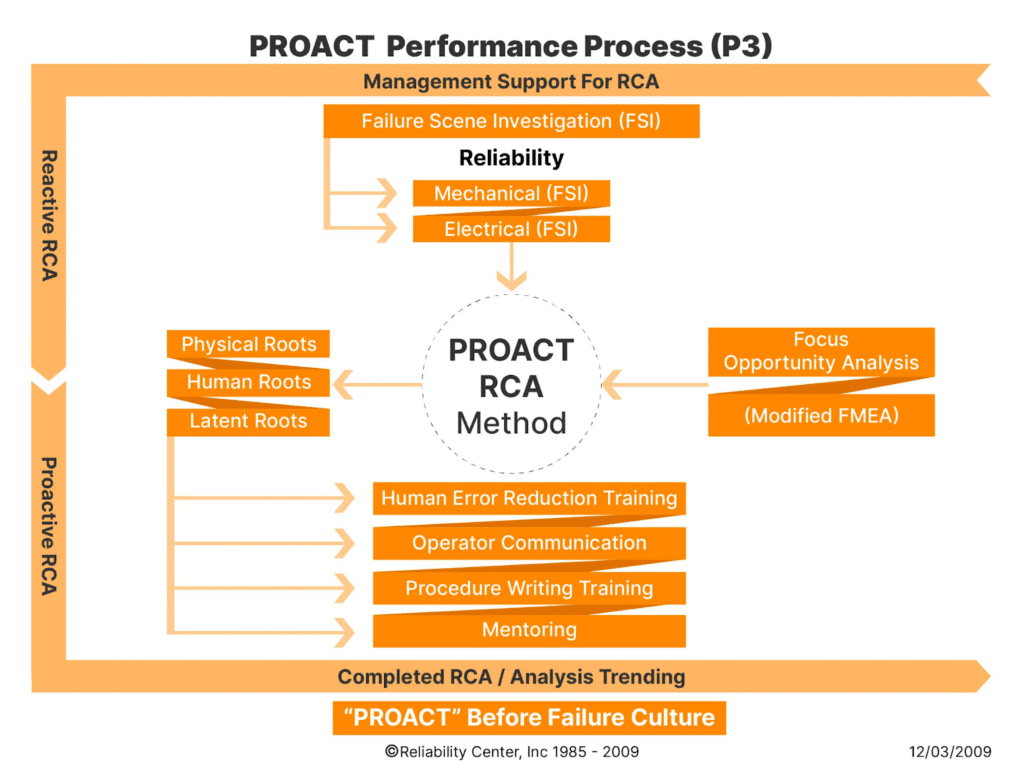
The key takeaway was the importance of a reliability-focused culture. By addressing human factors, improving procedures, and investing in the right tools, the facility turned a costly failure into a catalyst for positive change. The staff, once reactive, now embraced a proactive mindset, continuously seeking ways to prevent issues before they arose.
Conclusion
The chronic pump failure at Aberdeen 123 was more than a technical glitch; it was a lesson in the importance of reliability and proactive maintenance. Through the lens of Root Cause Analysis and the steadfast application of the PROACT® methodology, the facility resolved the immediate issue and also laid a stronger foundation for future reliability.
This case study underscores the transformative power of RCA in turning crises into opportunities. By making reliability a habit, facilities can enhance uptime, safety, and ROI, ensuring they are always prepared to face and overcome challenges. For more insights on improving your facility’s reliability through Root Cause Analysis, visit Reliability Center Inc. and explore our training and consulting services designed to help you achieve operational excellence.
___________
I hope you found this case study on a Chronic Pump Failure Causing Unexpected Shutdown insightful and actionable! Stay tuned for more thought-provoking articles as we continue to share our knowledge. Success is rooted in a thorough understanding and consistent application, and we hope this article was a step in unlocking the full potential of Root Cause Analysis for your organization.Reliability runs initiatives such as an online learning center focused on the proprietary PROACT® RCA methodology and EasyRCA.com software. For additional resources, visit EasyRCA Resources.
Ignite your curiosity, subscribe now!
Stay informed and connected with the latest updates by subscribing today!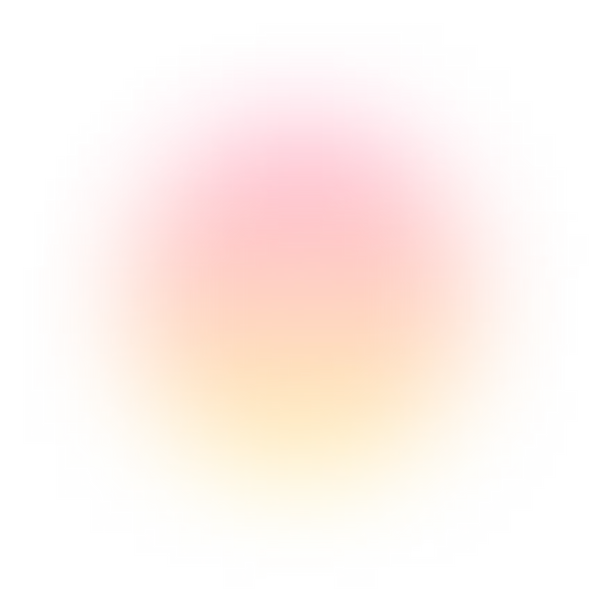
Recent Comments