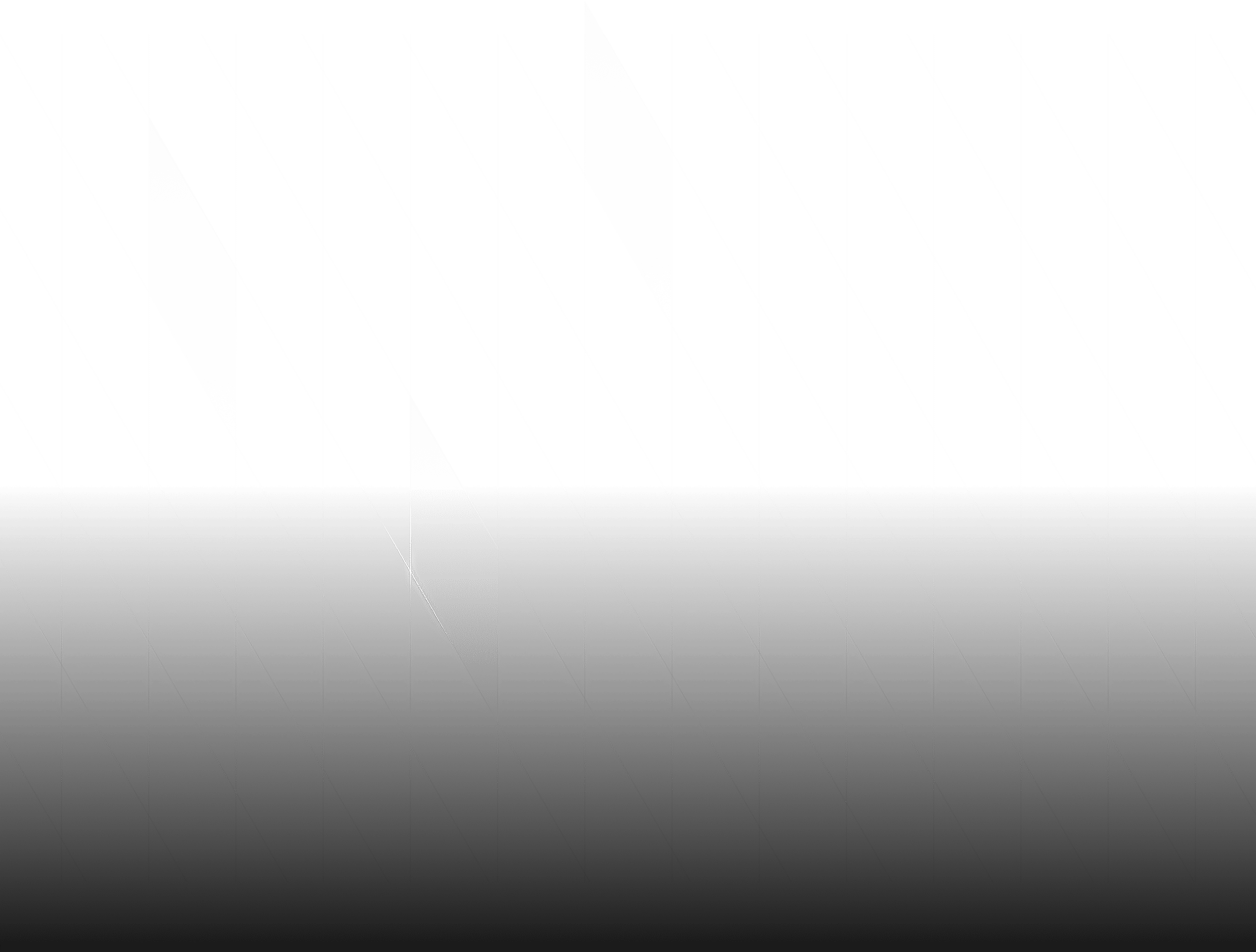
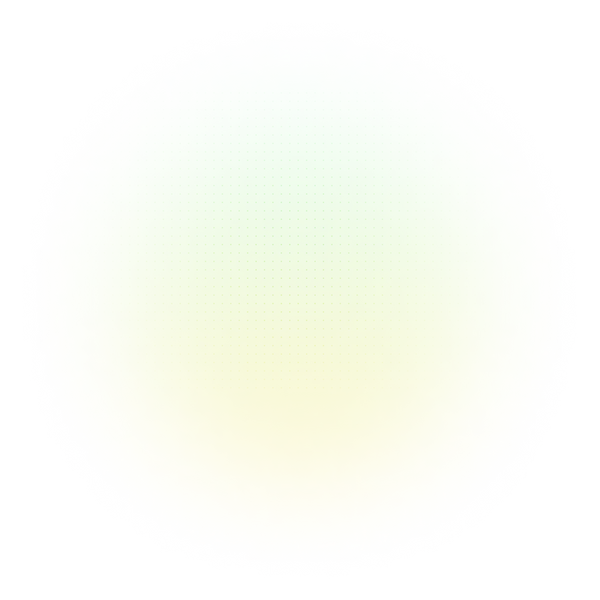

With over two decades in business – spanning strategy consulting, tech startups and executive leadership – I am committed to helping your organization thrive.
At Reliability, we’re on a mission to help enhance strategic decision-making and operational excellence through the power of Root Cause Analysis, and I hope this article will be helpful!
Our goal is to help you better understand real life case studies of reliability improvement by offering insights, case studies and practical tips based on years of experience. Whether you’re new to doing root cause analyses or a seasoned pro, we trust this will be useful in your journey towards working hard and working smart.
———————
In a Louisiana ammonia plant, downtime was a significant issue. With 116 days of downtime compared to an industry average of 49.5 days, this was the worst record for this type of facility globally. The primary issue was the repeated loss of the ammonia compressor, which happened twice in one year due to inadequate lead time information and improper monitoring practices.
The Incident
The plant unexpectedly lost the ammonia compressor twice within a year, severely impacting operations. The shutdowns were primarily due to the lack of continuous information about the equipment’s health, leading to unscheduled and unsafe shutdowns.
Disruption
For the plant management, the compressor failures were catastrophic. The facility, already running on a tight schedule, faced a domino effect of delays and increased pressure to meet customer orders. The downtime resulted in substantial financial losses and damaged the plant’s reputation for reliability.
Initial Findings
The initial investigation revealed that supervision was relying on once-a-month hand-held velocity readings to monitor equipment running at 36,000 rpm. This approach was inadequate for high-speed large equipment, leading to significant gaps in understanding the equipment’s health. The lack of continuous monitoring prevented early detection of issues and safe, timely shutdowns.
Detailed Analysis
The in-depth analysis of the plant’s operational challenges revealed several critical issues that were contributing to frequent failures and inefficiencies.
Key Issues Identified
- Inadequate Monitoring:
Reliance on monthly hand-held velocity readings for high-speed equipment was insufficient. Lacking continuous information created significant gaps in understanding equipment health.
- Ineffective Preventive Maintenance:
Preventive maintenance was often rescheduled to make up for lost production, leading to major breakdowns at critical times.
- Failed Predictive Maintenance:
Technicians did not take readings at scheduled intervals, causing catastrophic equipment failures. No trending was performed due to the lack of data, resulting in highly reactive work and inefficient repairs.
- Inadequate Root Cause Analysis:
Root Cause Analysis (RCA) often stops at identifying the broken component and assigning human blame without addressing system root causes.
- Poor Process Data Management:
Process data was often missing, inadequate, or misleading, preventing operators from seeing unfavorable trends.
- Inventory Management Issues:
High failure rates led to supervision hoarding parts, causing inefficiencies in part inventory management. Only high-speed equipment received proper balancing, while other equipment often had high vibration issues due to improper or no balancing.
Corrective Actions
To enhance the reliability and efficiency of our equipment, following was implemented several key strategies aimed at improving monitoring and maintenance practices. By introducing continuous monitoring, reinforcing preventive maintenance schedules, enhancing predictive maintenance protocols, conducting comprehensive root cause analysis, improving data management, and optimizing inventory management, addressed critical gaps and laid the foundation for sustained operational excellence. Below are the specific improvements made in each area.
Monitoring and Maintenance Improvements:
- Continuous Monitoring: Implemented radial eddy current proximity probes to measure shaft displacement 24/7, providing real-time data and preset alarm levels for decision-making.
- Scheduled Preventive Maintenance: Reinforced adherence to preventive maintenance schedules to avoid deferring essential tasks.
Enhanced Predictive Maintenance:
- Regular Data Collection: Established strict schedules for technicians to take and record readings, enabling effective trend analysis and early issue detection.
- Reactive Work Reduction: Minimized reactive work by ensuring regular monitoring and predictive maintenance tasks were completed.
Comprehensive Root Cause Analysis:
- Systemic RCA: Employed PROACT® methodology to conduct thorough RCA, identifying not just physical and human roots but also system roots for long-term solutions. This is where EasyRCA can be an invaluable tool for streamlining the process.
Improved Data Management:
- Accurate Process Data: Ensured accurate and complete data collection to help operators identify and address approaching unfavorable trends.
Efficient Inventory Management:
- Centralized Part Inventory: Standardized part inventory management to eliminate hoarding and ensure the availability of necessary parts.
- Proper Balancing: Ensured all equipment, not just high-speed, received proper balancing to reduce vibration issues.
Results
The plant achieved a dramatic reduction in downtime, initially cutting it to 19.4 days within the first year, which was recognized as the best in the world. This impressive feat was further improved upon, reducing downtime to just 10 days after two years. Such a significant decrease in downtime not only boosted operational efficiency but also played a crucial role in minimizing production disruptions and enhancing overall productivity.
In addition to the remarkable downtime reduction, the plant realized significant cost savings over a three-year period. By implementing more effective root cause analysis and maintenance practices, the plant was able to optimize its operations and reduce unnecessary expenses. These efforts led to net dollar savings of $36,000,000, highlighting the financial benefits of investing in comprehensive reliability and maintenance strategies. This substantial cost saving improved the plant’s profitability and underscored the value of proactive maintenance and thorough root cause analysis in driving long-term operational excellence.
Conclusion
This case study demonstrates how a proactive approach using the PROACT® RCA methodology can transform an organization’s reliability and operational efficiency. By addressing core issues and implementing strategic solutions, the Louisiana ammonia plant overcame its challenges and set a new standard in downtime reduction and cost savings.
At Reliability Center Inc., we believe in turning crisis into opportunities through comprehensive RCA. For more insights and to enhance your facility’s reliability, explore our PROACT® RCA training and consulting services designed to help you achieve operational excellence.
___________
I hope you found this case study insightful and actionable! Stay tuned for more thought-provoking articles as we continue to share our knowledge. Success is rooted in a thorough understanding and consistent application, and we hope this article was a step in unlocking the full potential of Root Cause Analysis for your organization.
Reliability runs initiatives such as an online learning center focused on the proprietary PROACT® RCA methodology and EasyRCA.com software. For additional resources, visit EasyRCA Resources.
Ignite your curiosity, subscribe now!
Stay informed and connected with the latest updates by subscribing today!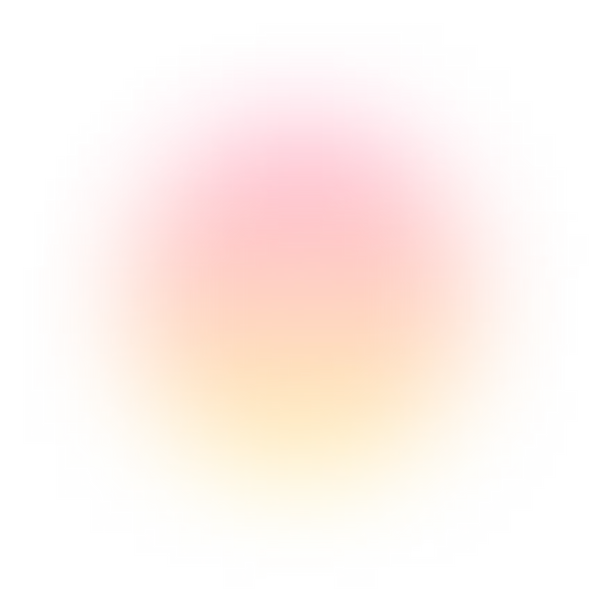
Recent Comments