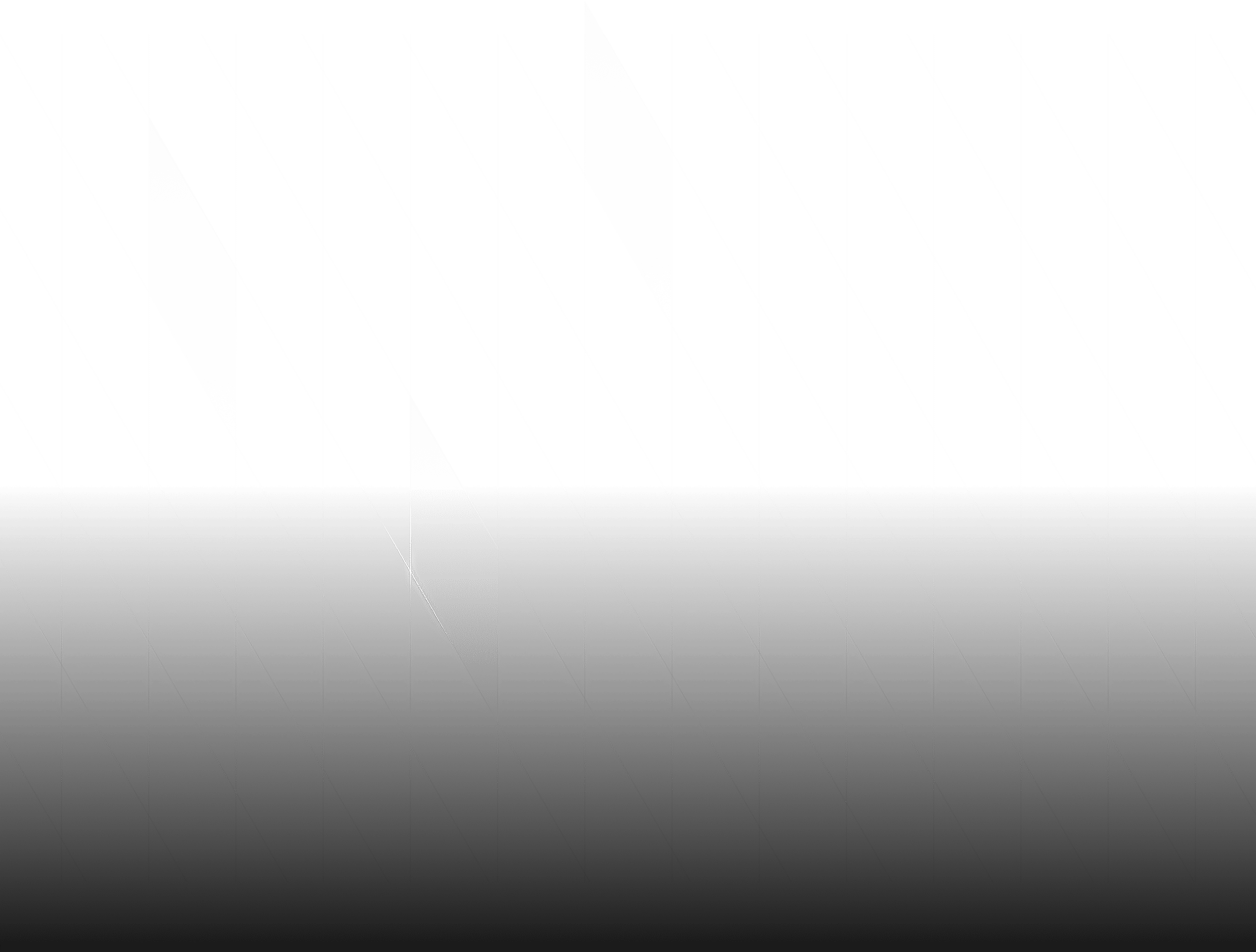
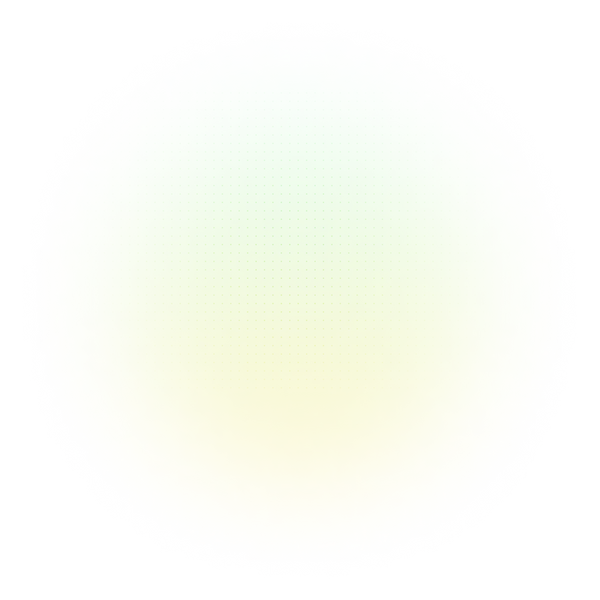

With over two decades in business – spanning strategy consulting, tech startups and executive leadership – I am committed to helping your organization thrive.
At Reliability, we’re on a mission to help enhance strategic decision-making and operational excellence through the power of Root Cause Analysis, and I hope this article will be helpful!
Our goal is to help you better understand Limitations of 5 Whys Analysis and ways to avoid them by offering insights and practical tips based on years of experience. Whether you’re new to doing root cause analyses or a seasoned pro, we trust this will be useful in your journey towards working hard and working smart.
———————
The 5 Whys technique, a staple in root cause analysis, originated at Toyota and has been widely adopted in lean manufacturing. In this article, we have covered the 5 Whys method in detail. In short, this method involves asking “Why?” five times or more to peel back the layers of symptoms, aiming to uncover the root cause of a problem.
What are the advantages of the 5 Whys technique?
Simplicity and Ease of Use
The 5 Whys doesn’t require advanced statistical tools like data segmentation, hypothesis testing, or regression. It’s straightforward and can often be conducted without a detailed data collection plan.
Quick Application
This method allows for rapid identification of root causes, making it a practical tool for problem-solving in various settings.

Limitations of 5 Whys:
- Potential for Missing the Root Cause: The 5 Whys may not always lead to the true root cause, especially when the cause is complex or unknown.
- Oversimplification: It often assumes a linear relationship where each symptom is linked to a single cause, which may not always be the case.
- Skill-Dependent: The effectiveness of the 5 Whys largely depends on the skill and experience of the person conducting it.
- Lack of Repeatability: Different individuals may arrive at different conclusions when applying the 5 Whys to the same problem.
- Confusion between Causal Factors and Root Causes: The method sometimes struggles to distinguish between what is merely a contributing factor and what is the actual root cause.
- Insufficient Rigour: There’s often no requirement to empirically test the root causes identified, leading to potentially unsubstantiated conclusions.
- Bias and Subjectivity: The process can be skewed by personal biases or hierarchical influences, leading to misleading outcomes.
- Over-reliance on Deduction: In the absence of direct observation, the method can devolve into a series of deductions rather than an analysis based on facts.
Strategies to Enhance the Effectiveness of the 5 Whys Technique:
The 5 Whys Techniques can be enhanced through the following strategies:
Training Can Enhance the Effectiveness:
Proper training in the 5 Whys technique is a cornerstone of its effectiveness. When practitioners are well-trained, they possess the ability to delve deeper into issues, uncovering a broader range of problems and their underlying causes. This depth of understanding is crucial for implementing meaningful and lasting improvements.
Training equips individuals with the necessary skills to ask the right questions, interpret the answers effectively, and navigate the complexities that often accompany root cause analysis. The goal is to move beyond superficial understanding to a level where significant and impactful solutions can be developed.
Emphasising Observation Over Deduction:
On-Site Observation
The principle of on-site observation involves directly observing the processes and conditions where the problem occurred. By being physically present at the site of the issue, practitioners gain a more accurate and comprehensive understanding of the problem. This direct observation ensures that the analysis is grounded in reality, rather than theoretical or removed from the actual conditions.
Evidence-Based Conclusions
For each level of “Why?” posed during the analysis, it is essential that the conclusions drawn are supported by factual evidence. This evidence should be gathered through direct observation and data collection. The aim is to base each step of the analysis on solid facts, thereby avoiding assumptions and conjectures. This approach ensures that each identified cause is not just a theoretical possibility but is backed by real-world evidence.
Timeline Analysis:
Understanding the chronological sequence of events that led to a problem is a critical aspect of root cause analysis. This timeline analysis helps in mapping out the entire scenario in which the issue occurred, providing valuable context.
This aids in identifying each causal factor that contributed to the problem. With this understanding, the 5 Whys, or other analytical tools, can be more effectively applied to each factor, leading to a more comprehensive and accurate identification of the root causes.
Coupling with Risk Assessment:
Integrating a simple risk assessment with the 5 Whys methodology enhances its effectiveness. This combination is particularly useful when there is uncertainty about whether the identified cause is indeed the root cause. A risk assessment can evaluate the potential impacts of the problem recurring if the identified cause is not accurately addressed. This process helps in deciding whether a more in-depth analysis is necessary, ensuring that critical issues are not overlooked.
Developing Effective Countermeasures:
The development of countermeasures in response to identified root causes is a crucial step. These countermeasures should be designed to address the system or process level issues that have been identified. The focus should be on creating solutions that prevent the recurrence of the problem, rather than merely addressing its symptoms. Effective countermeasures are preventive in nature, ensuring that once a problem is resolved, it does not re-emerge.
Considering More Robust Methods for Critical Issues:
In situations where the stakes are high, and the risk of failure is significant, more robust methods than the 5 Whys may be necessary. Techniques such as Failure Mode and Effects Analysis (FMEA) offer a more systematic and thorough approach to root cause analysis. These methods are particularly useful in complex scenarios where the potential consequences of failure are severe. They provide a structured way to identify and address problems, ensuring a comprehensive and reliable solution.
Conclusion
While the 5 Whys is a valuable tool in root cause analysis, its effectiveness depends on how it’s applied. Understanding its limitations and integrating it with other methods and observational techniques can significantly enhance its utility in problem-solving.
By addressing the above limitations and leveraging digital tools, such as data collection and analysis such as EasyRCA, organizations can enhance their problem-solving efforts. The integration of digital platforms not only streamlines the root cause analysis process but also improves the accuracy of identifying underlying issues.
___________
I hope you found this guide to limitations of 5 Whys and how to avoid them insightful and actionable! Stay tuned for more thought-provoking articles as we continue to share our knowledge. Success is rooted in a thorough understanding and consistent application, and we hope this article was a step in unlocking the full potential of Root Cause Analysis for your organization.
Reliability runs initiatives such as an online learning center focused on the proprietary PROACT® RCA methodology and EasyRCA.com software. For additional resources, visit EasyRCA Resources.
Ignite your curiosity, subscribe now!
Stay informed and connected with the latest updates by subscribing today!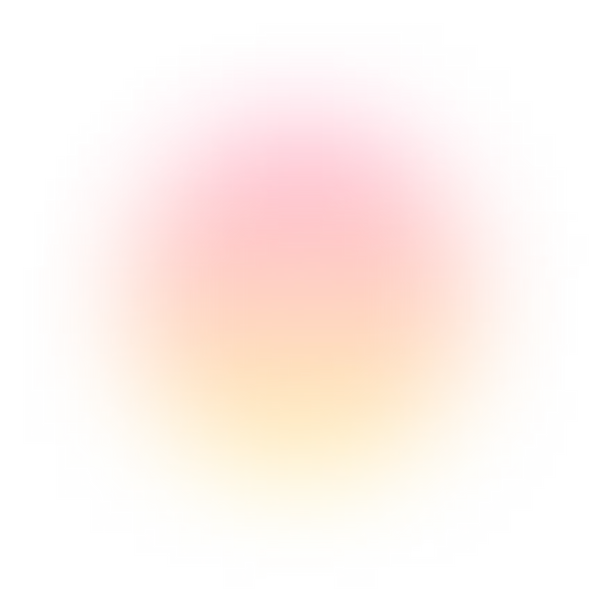
Recent Comments