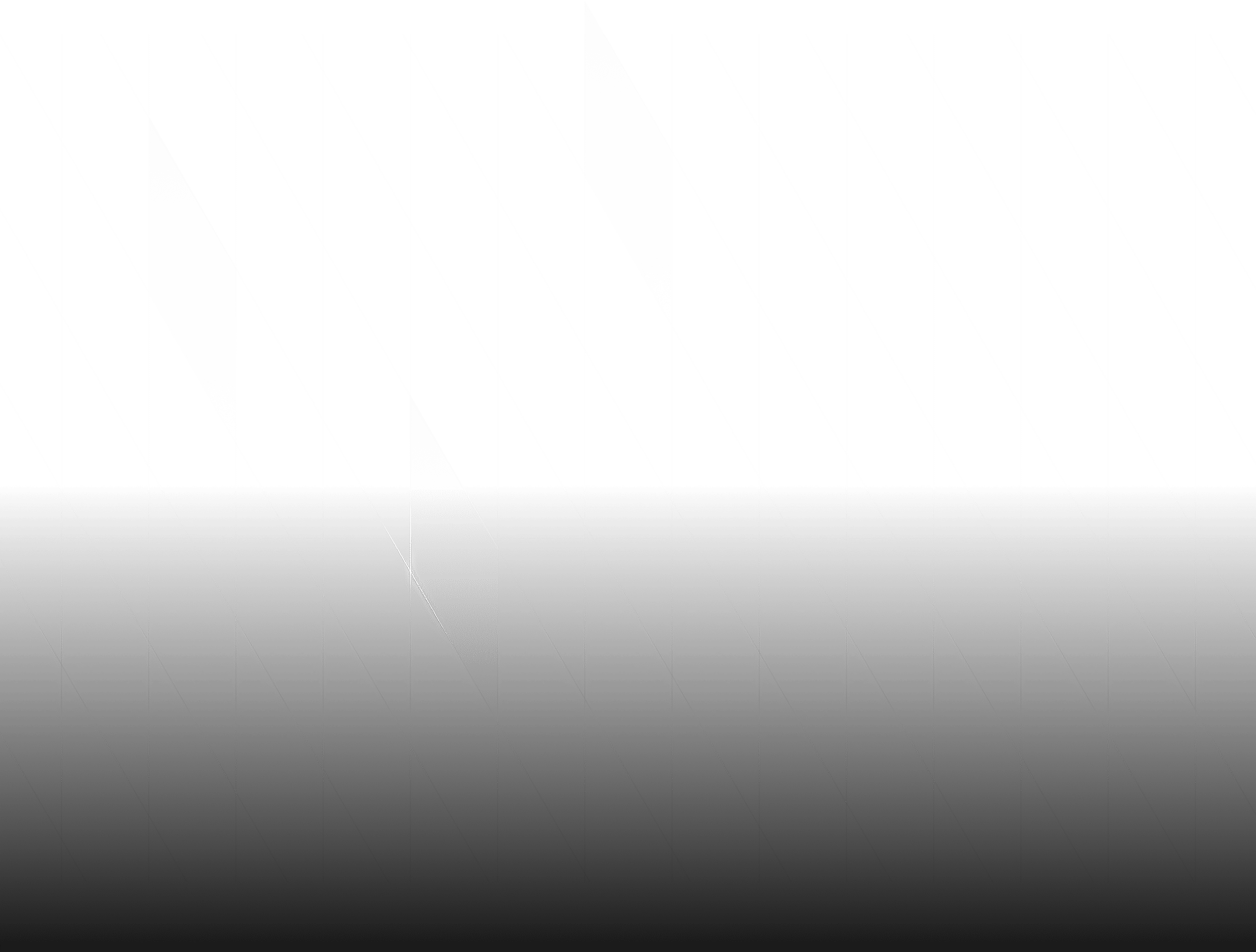
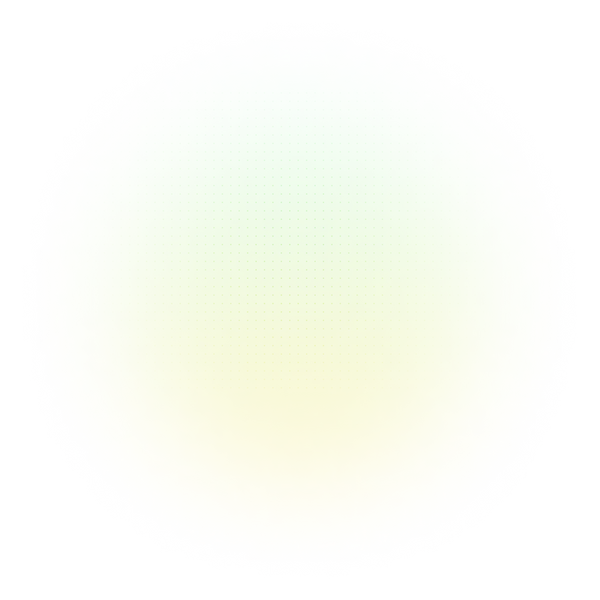

With over two decades in business – spanning strategy consulting, tech startups, and executive leadership – I am committed to helping your organization thrive.
At Reliability, we’re on a mission to help enhance strategic decision-making and operational excellence through the power of Root Cause Analysis, and I hope this article will be helpful!
Our goal is to help you better understand preventative maintenance by offering insights, case studies, and practical tips based on years of experience. Whether you’re new to doing root cause analyses or a seasoned pro, we trust this will be useful in your journey towards working hard and working smart.
____________________________________________________________________
Equipment downtime, whether in manufacturing plants, fleet management, or IT infrastructure, can lead to significant losses. One of the most effective strategies to combat downtime is preventative maintenance. By addressing potential issues before they become real problems, businesses can not only reduce downtime but also enhance efficiency and boost their bottom line. A prime example of the consequences of neglecting preventative maintenance is highlighted in our Ammonia Case Study article.
What is Preventative Maintenance?
Preventative maintenance is a proactive approach to equipment management. Unlike reactive maintenance, which only addresses issues after they cause disruptions, preventative maintenance focuses on regular inspections, servicing, and repairs. These tasks are scheduled based on time, usage, or specific conditions observed during routine checks. This approach ensures that potential problems are identified and resolved before they escalate, keeping equipment in optimal working condition.
Aspect | With Preventative Maintenance | Without Preventative Maintenance |
Downtime | Minimal, with fewer unexpected breakdowns and disruptions. | Frequent, due to unexpected equipment failures and repairs. |
Equipment Lifespan | Extended, as regular maintenance prevents wear and tear. | Shortened, as lack of maintenance leads to accelerated degradation. |
Maintenance Costs | Lower overall costs, with planned and predictable expenses. | Higher overall costs, with expensive emergency repairs. |
Operational Efficiency | High, with consistent and reliable equipment performance. | Low, due to frequent interruptions and inefficiencies. |
Safety | Improved, with reduced risk of accidents and injuries. | Compromised, with increased likelihood of accidents. |
Productivity | Enhanced, as equipment runs smoothly and reliably. | Decreased, due to regular downtime and repair needs. |
Budget Predictability | High, with maintenance costs planned and controlled. | Low, with unpredictable and often high repair costs. |
Employee Morale | Higher, as workers are less stressed by equipment failures. | Lower, due to frustration and stress from frequent breakdowns. |
Long-Term ROI | Higher, with better asset utilization and reduced replacement needs. | Lower, due to frequent equipment replacements and inefficiencies. |
Environmental Impact | Lower, as well-maintained equipment tends to be more energy-efficient and have fewer emissions. | Higher, due to inefficient equipment operation and potential for greater emissions. |
Table 1: comparison between using preventative maintenance and not using preventative maintenance.
The Benefits of Preventative Maintenance:
- Reduced Downtime:
Preventative maintenance significantly reduces unexpected equipment failures that can halt operations. By identifying and fixing small issues early, businesses can avoid costly interruptions and ensure consistent productivity. - Increased Equipment Lifespan:
Regular maintenance helps extend the lifespan of equipment. By routinely checking and servicing components, businesses can minimize wear and tear, getting more value from their investments and reducing the need for frequent replacements. - Cost Savings:
While preventative maintenance requires an initial investment, it leads to long-term savings. Avoiding emergency repairs and unplanned downtime not only cuts costs but also enhances overall operational efficiency. - Improved Safety:
Well-maintained equipment is less likely to malfunction, reducing the risk of accidents in the workplace. This not only protects employees but also mitigates legal and financial risks associated with workplace injuries. - Enhanced Productivity:
Reliable equipment allows employees to focus on their tasks without interruptions. A smooth, uninterrupted workflow boosts productivity, as workers spend less time dealing with equipment failures and more time contributing to the company’s success.
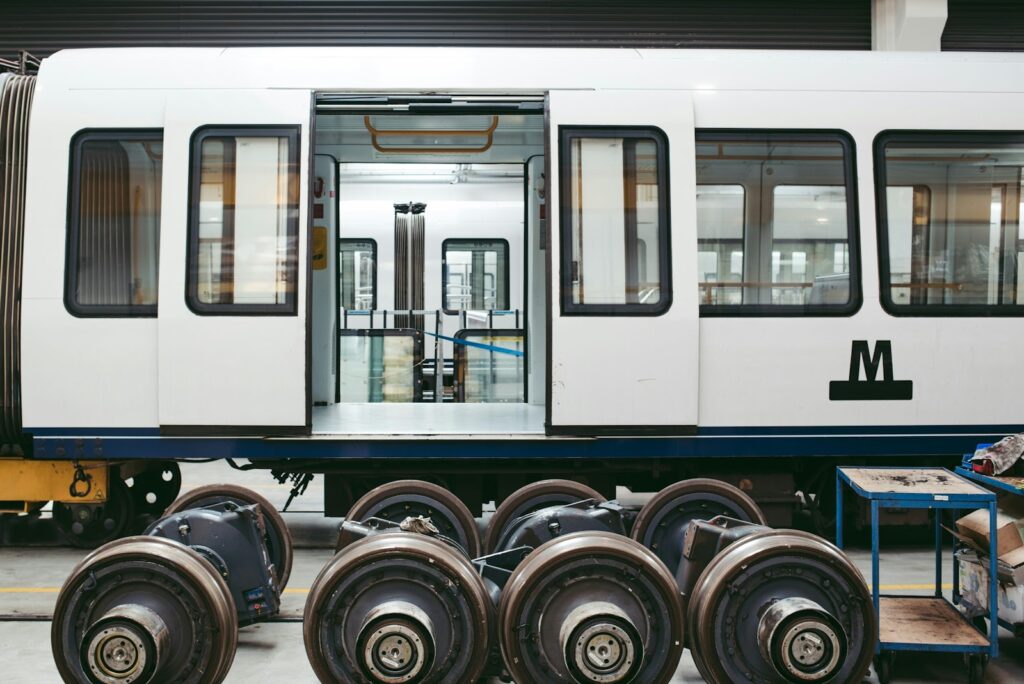
Implementing a Preventative Maintenance Program
To maximize the benefits of preventative maintenance, businesses should implement a structured program. Here’s how:
- Inventory and Assessment
Start by cataloging all equipment and assessing its condition, usage, and importance to operations. This helps prioritize maintenance tasks based on the criticality of each piece of equipment. - Develop a Maintenance Schedule
Create a maintenance schedule tailored to your equipment’s needs, considering manufacturer recommendations, usage patterns, and your initial assessments. Include essential tasks like lubrication, calibration, and parts replacement. - Assign Responsibilities
Clearly define who is responsible for each maintenance task, whether it’s in-house technicians or third-party service providers. Ensure that all involved personnel are properly trained and equipped to perform their duties effectively. - Monitor and Record Activities
Keep detailed records of all maintenance activities, including inspections and repairs. This documentation is crucial for tracking equipment history, identifying recurring issues, and informing future maintenance decisions. - Continuous Improvement
Regularly review and refine your preventative maintenance program. Analyze maintenance records to spot trends and address gaps, ensuring that your strategy evolves with your business needs.
Conclusion
Preventative maintenance is a vital strategy for reducing downtime and maximizing productivity. By investing in regular maintenance, businesses can avoid unexpected failures, extend equipment lifespan, and create a safer, more efficient work environment. A well-structured preventative maintenance program is not just about saving costs; it’s an investment in the long-term success of your operations.
_________________________________________________________
I hope you found this case study insightful and actionable! Stay tuned for more thought-provoking articles as we continue to share our knowledge. Success is rooted in a thorough understanding and consistent application, and we hope this article was a step in unlocking the full potential of Root Cause Analysis for your organization.
Reliability runs initiatives such as an online learning center focused on the proprietary PROACT® RCA methodology and EasyRCA.com software. For additional resources, visit EasyRCA Resources.
Ignite your curiosity, subscribe now!
Stay informed and connected with the latest updates by subscribing today!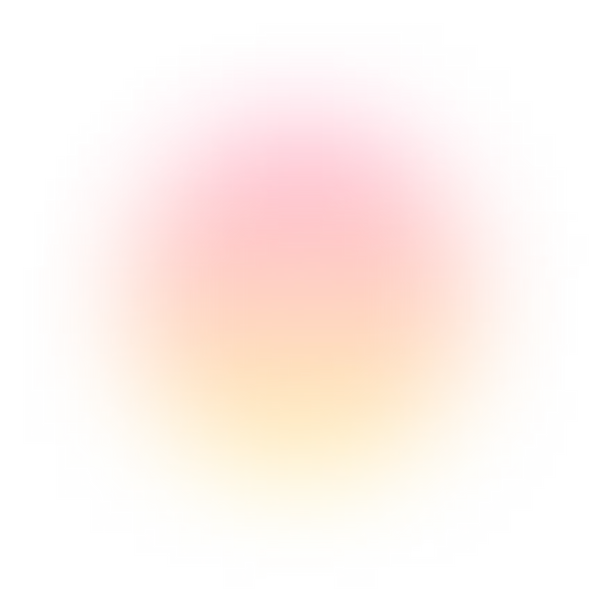
Recent Comments