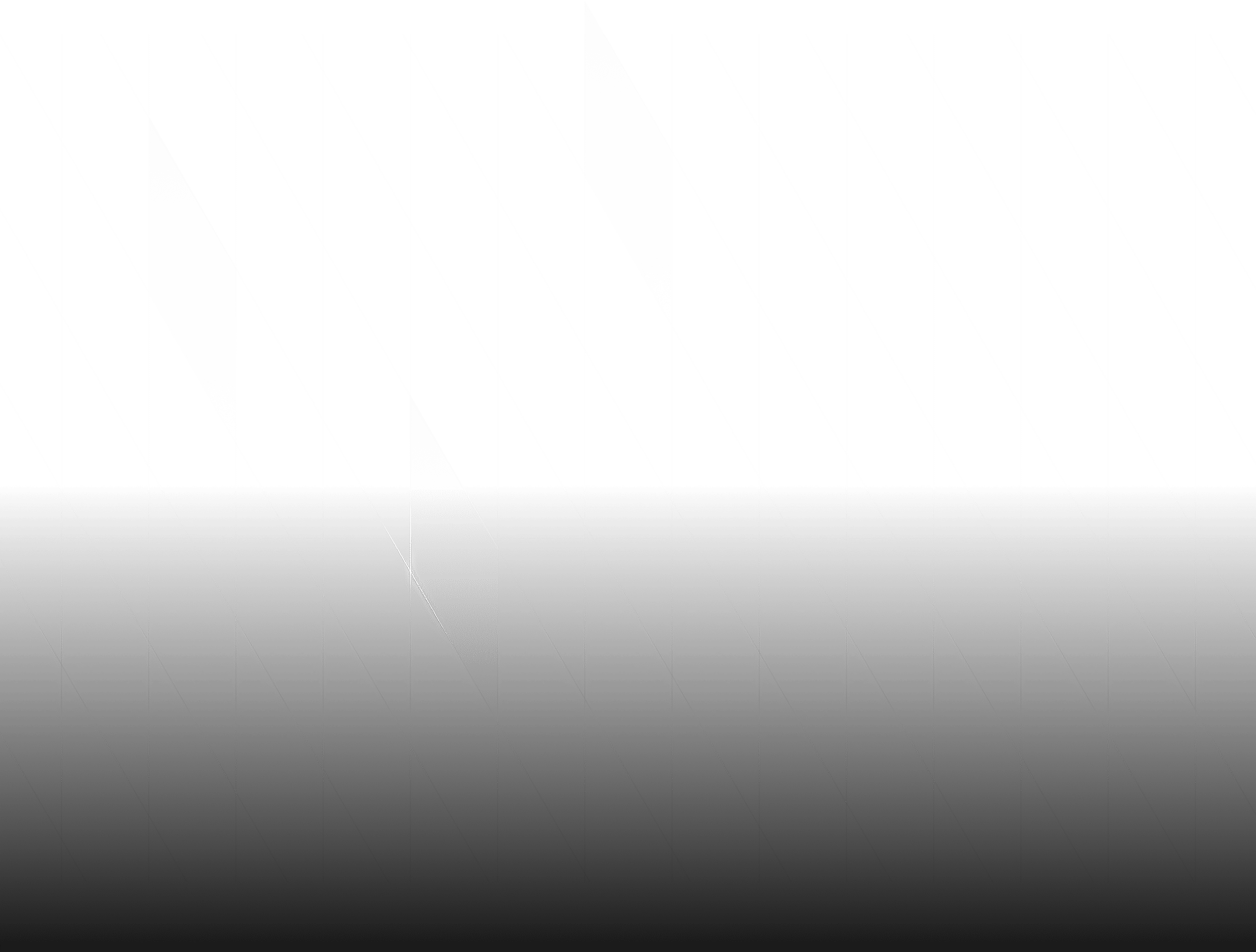
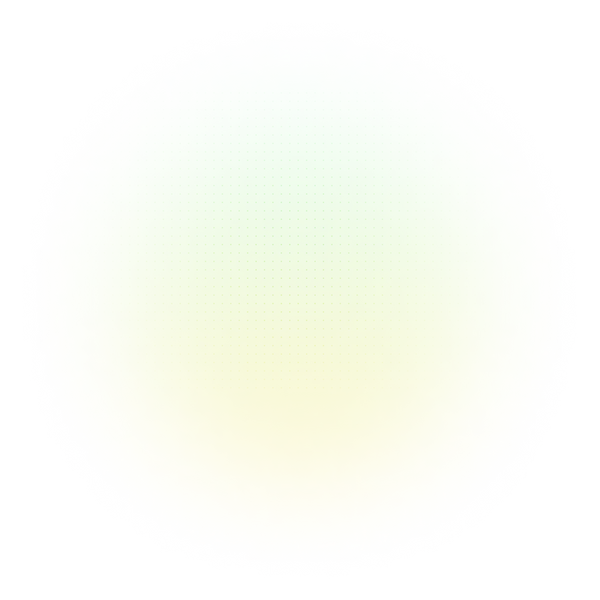

Problems are a part of every business, but the ability to resolve issues effectively is what sets successful organizations apart from the rest. One powerful tool for getting to the depths of the problems and solving them is Root Cause Analysis (RCA). By looking beyond the symptoms and identifying the deeper causes of problems, RCA helps prevent problems from recurring, ensuring long-term solutions. This blog post acts as a guide on how to create a comprehensive RCA template that can be adapted by any industry for any problem.
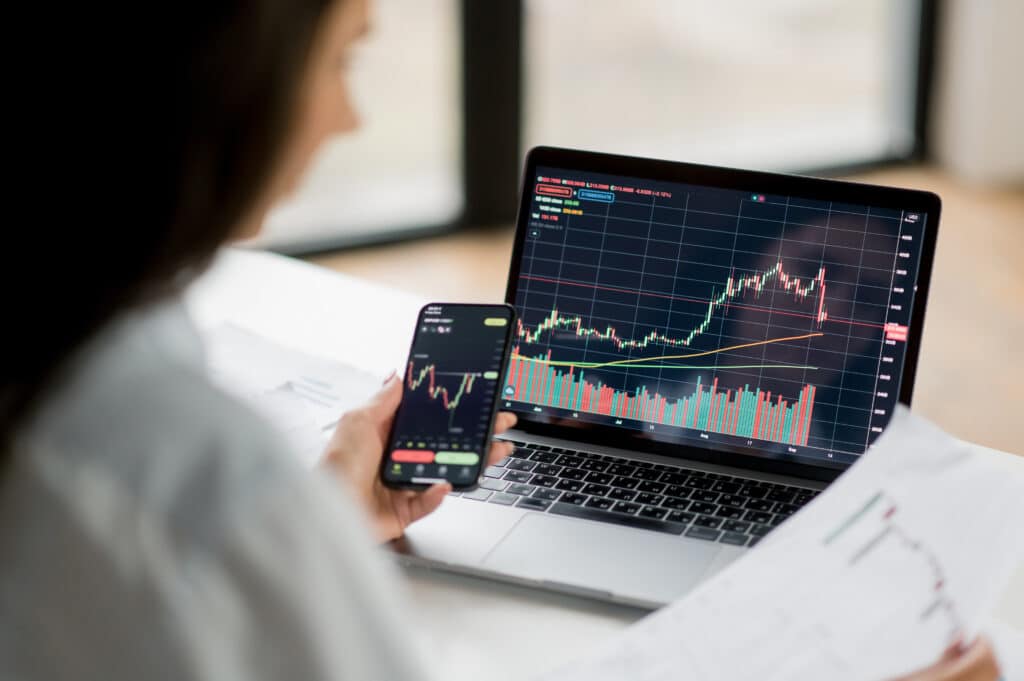
What is Root Cause Analysis (RCA)?
Root Cause Analysis (RCA) is a systematic process designed to identify the underlying reasons for a problem. Instead of just treating the symptoms, RCA helps us identify the source or cause of the “illness”.
RCA is commonly used in various industries, such as manufacturing, healthcare, and IT, where it’s crucial to keep operations running smoothly. For example, if a machine breaks down, instead of just repairing it, RCA would look at why it broke in the first place. Was it a maintenance issue? Did a part fail? By understanding the cause, steps can be taken to fix the problem at its original source.
Why You Need an RCA Template
Using a ready-made RCA template makes it easier for your team to tackle problems. It ensures that nothing gets missed and that everyone can contribute. With a clear format, tracking and implementing solutions becomes more straightforward and consistent.
Here’s a Step-by-Step Guide to Creating Your RCA Template:
1. Define the Problem.
The first step in any RCA is to clearly define the problem. A well-defined problem statement keeps your analysis focused. For example, production delay on factory line A. Make sure your problem description is specific, measurable, and observable.
2. Describe the Impact.
Next, describe how the problem impacts the business. This step ensures that stakeholders understand the urgency of resolving the issue. For example, the production delay resulted in a 20% reduction in daily output, leading to missed customer deadlines.
3. Gather Data and Evidence.
Collect relevant and factual data related to the problem. This may include timelines, specific events, machine logs, or other related information. For example, a machine malfunction occurred at 2 PM, causing a 4-hour production stop. Always rely on objective data to avoid assumptions.
4. Identify Possible Causes
List all possible causes for the problem. Techniques like brainstorming, the 5 Whys, or a fishbone diagram can help identify potential root causes. For example, why did production stop? The machine broke down. Why did the machine break down? It wasn’t maintained on schedule.
5. Analyze and Prioritize Root Causes.
Once all potential causes are listed, it’s time to analyze the data and pinpoint the actual root cause(s). This step ensures you’re targeting the right issue. For example, the root cause is a missed scheduled maintenance due to a shortage of maintenance staff.
6. Develop Corrective Actions.
Now that you’ve identified the root cause, propose actionable solutions. These should directly address the root cause to prevent recurrence. For example, hire additional maintenance staff and implement an automated reminder system.
7. Assign Responsibilities
Ensure accountability by assigning specific team members to the corrective actions. Each person should know their role in resolving the issue. For example, assign the maintenance team to oversee the new automated schedule and ensure compliance.
8. Set Timelines
Establish clear deadlines for implementing corrective actions. This step ensures that solutions are executed promptly. For example, the hiring of new staff should be completed within 30 days.
9. Monitor and Follow-Up
Finally, ensure the effectiveness of your corrective actions by monitoring the results over time. Regular check-ins can help you adjust the solution if necessary. For example, review machine performance weekly for the next three months to ensure no further delays.
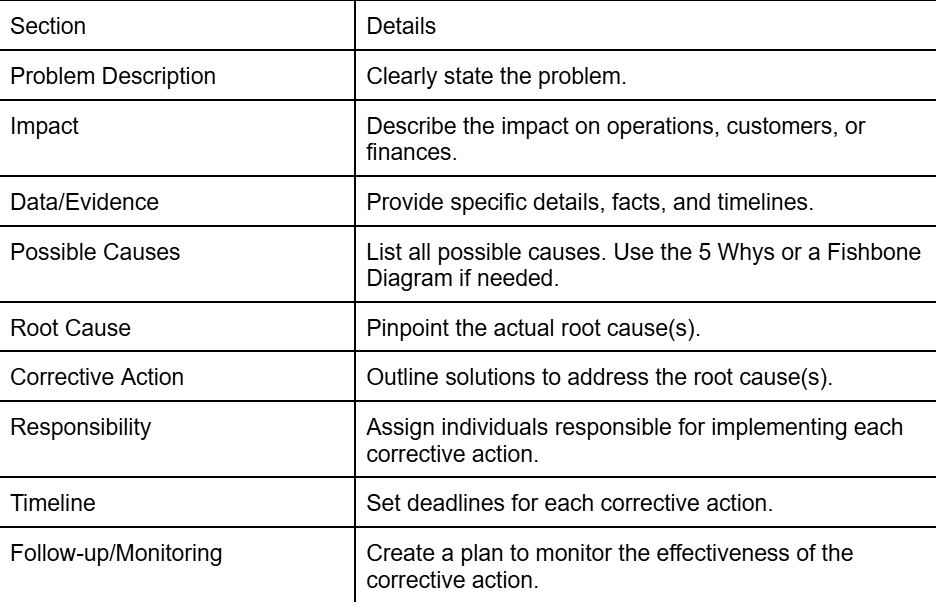
Conclusion
A well-designed RCA template is an invaluable tool for any organization aiming to enhance problem-solving and prevent future issues, particularly over the long term. By following this step-by-step guide, you can create a template tailored to your team’s needs, ensuring that you address the true root causes of problems rather than just the symptoms. This approach not only boosts operational efficiency but also helps maintain higher standards of quality and productivity.
Now that you know how to create a Root Cause Analysis template, it’s time to put it into action the next time a problem arises in your organization. Embrace this opportunity to strengthen your problem-solving capabilities and drive lasting improvements.
Ignite your curiosity, subscribe now!
Stay informed and connected with the latest updates by subscribing today!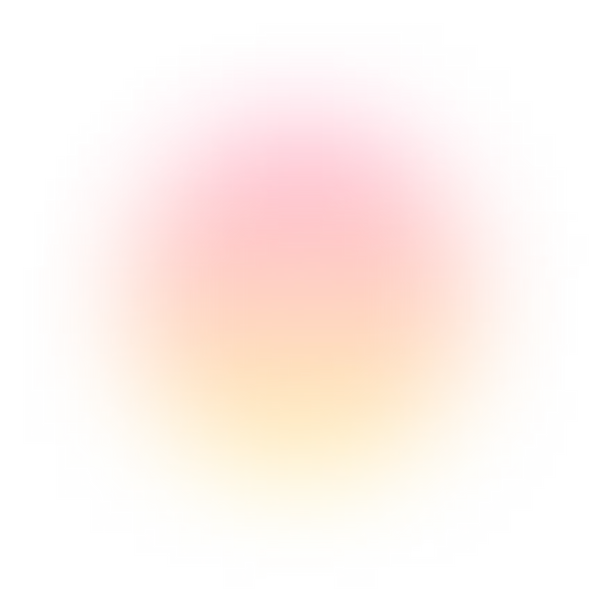
Recent Comments