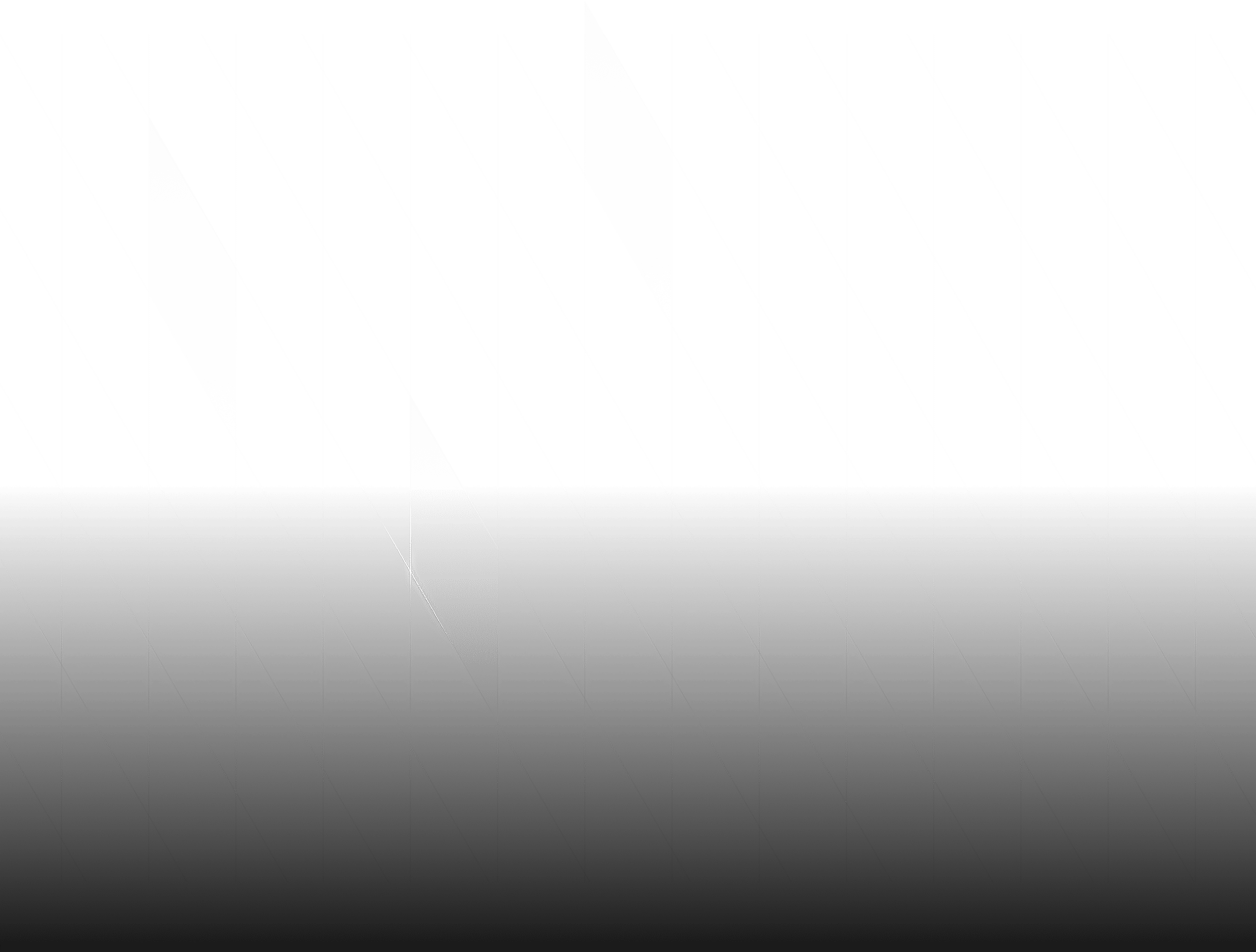
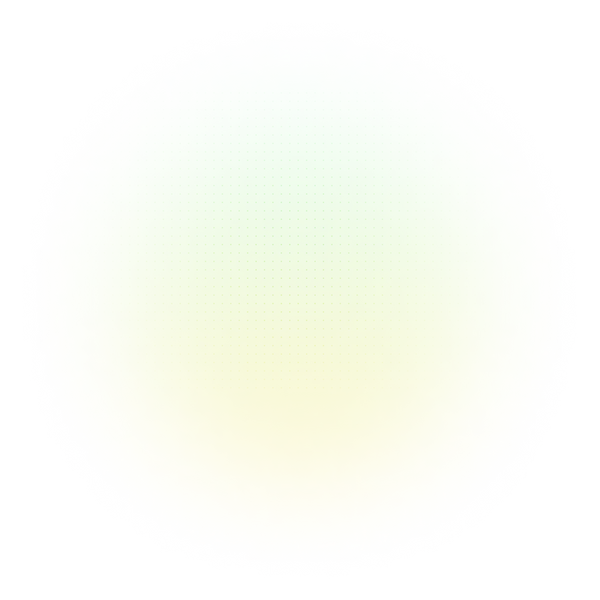

With over two decades in business – spanning strategy consulting, tech startups and executive leadership – I am committed to helping your organization thrive.
At Reliability, we’re on a mission to help enhance strategic decision-making and operational excellence through the power of Root Cause Analysis, and I hope this article will be helpful!
Our goal is to help you better understand real life case studies of reliability improvement by offering insights, case studies and practical tips based on years of experience. Whether you’re new to doing root cause analyses or a seasoned pro, we trust this will be useful in your journey towards working hard and working smart.
———————
A nylon plant located in Virginia was a key supplier for the tire and carpet industries. The plant had significant operational challenges that threatened its productivity and safety.
Despite its design capacity of 334,000,000 lbs. annually, the plant’s highest demonstrated production was only 319,000,000 lbs. Severe deterioration of plant structures and machinery, coupled with high downtime and overtime rates, necessitated a comprehensive reliability assessment.
How Did RCA Transformed The Plant?
Root Cause Analysis (RCA) played a pivotal role in identifying and addressing the underlying issues affecting the plant’s performance. By using the PROACT® methodology, the reliability department was able to systematically investigate the problems, uncover their root causes, and implement effective solutions.
Initial Findings
Upon research, the reliability team noticed the plant faced significant operational challenges, producing lower than capacity due to deteriorating machinery and structures. High downtime and overtime have increased injury rates and stress. Inadequate root cause analyses and poor maintenance practices result in unexpected outages, while inefficient planning and a disorganized spare parts inventory hinder decision-making and efficiency. Here is the breakdown of the initial findings:
- Production Shortfalls: The plant was consistently falling short of its production capacity, achieving only 319,000,000 lbs. annually.
- Machinery Deterioration: Plant structures and machinery had severely deteriorated, exacerbating operational inefficiencies.
- High Downtime and Overtime: Downtime exceeded 15%, and overtime was at 17%, leading to increased injury rates and operational stress.
- Inadequate Root Cause Analyses: Root cause analyses lacked depth, failing to address systemic issues.
- Poor Preventive and Predictive Maintenance: Preventive maintenance activities were frequently rescheduled, and predictive maintenance was not conducted at scheduled intervals, leading to unexpected outages.
- Inefficient Planning and Scheduling: Reactive work overwhelmed planners and the spare parts inventory was disorganized, causing supervisors to hoard parts and hindering efficient decision-making.
Solution
The reliability department conducted a thorough assessment and recommended several corrective actions to address the root causes of these issues. These included:
- Enhanced RCA Practices: Improving the depth and quality of root cause analyses to address systemic failures.
- Proper Execution of Maintenance Activities: Ensuring preventive and predictive maintenance activities were executed as scheduled to prevent unexpected failures.
- Efficient Planning and Scheduling: Streamlining planning and scheduling processes to manage reactive downtime more effectively.
- Organized Spare Parts Inventory: Implementing a system to manage spare parts inventory, reducing the need for supervisors to hoard parts and ensuring availability for maintenance needs.
- Empowered Decision-Making: Restoring decision-making authority to the personnel with the most field knowledge.
Results
The implementation of these recommendations led to remarkable improvements in the plant’s performance. By addressing systemic issues through more thorough analyses, the frequency of recurring problems decreased. Maintenance activities were consistently executed on schedule, leading to fewer unexpected failures and reduced downtime:
Increased Production: The plant produced 369,000,000 lbs. in the first year after the changes were implemented.
High Uptime: Achieved 98% uptime over 10 years, including scheduled turnarounds.
Reduced Maintenance Costs: Maintenance costs were reduced by 40%.
Lower Overtime: Maintenance overtime dropped to 4%-5% over 10 years.
Safety Improvements: The plant won the Corporation’s “President’s Safety Award” for significant safety improvements.
Financial Benefits: Net dollar benefits were estimated at $96,000,000.
Conclusion
The case study highlights the transformative power of a structured and thorough root cause analysis using the PROACT® methodology. Through root cause analyses, consistent maintenance execution, efficient planning, organized inventory management, and empowered decision-making, the plant has overcome significant operational challenges.
By addressing systemic issues and implementing proactive strategies, the nylon plant not only overcame its immediate challenges but also established a foundation for long-term reliability and operational excellence.
Key Takeaways
- Proactive Maintenance: Consistent and well-executed preventive and predictive maintenance can significantly reduce unexpected outages and improve operational efficiency.
- Comprehensive RCA: In-depth root cause analyses are crucial for identifying and addressing systemic issues, leading to sustainable improvements.
- Efficient Resource Management: Proper planning, scheduling, and inventory management are essential for maintaining high productivity and minimizing downtime.
- Safety and Reliability: Enhancing reliability practices not only improves production but also significantly enhances workplace safety.
For more insights on improving your facility’s reliability through Root Cause Analysis, visit Reliability Center Inc. and explore our training and consulting services designed to help you achieve operational excellence.
___________
I hope you found this case study insightful and actionable! Stay tuned for more thought-provoking articles as we continue to share our knowledge. Success is rooted in a thorough understanding and consistent application, and we hope this article was a step in unlocking the full potential of Root Cause Analysis for your organization.
Reliability runs initiatives such as an online learning center focused on the proprietary PROACT® RCA methodology and EasyRCA.com software. For additional resources, visit EasyRCA Resources.
Ignite your curiosity, subscribe now!
Stay informed and connected with the latest updates by subscribing today!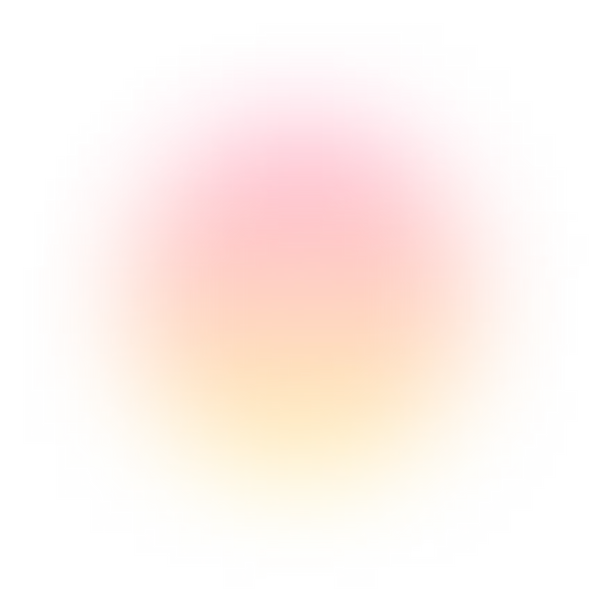
Recent Comments