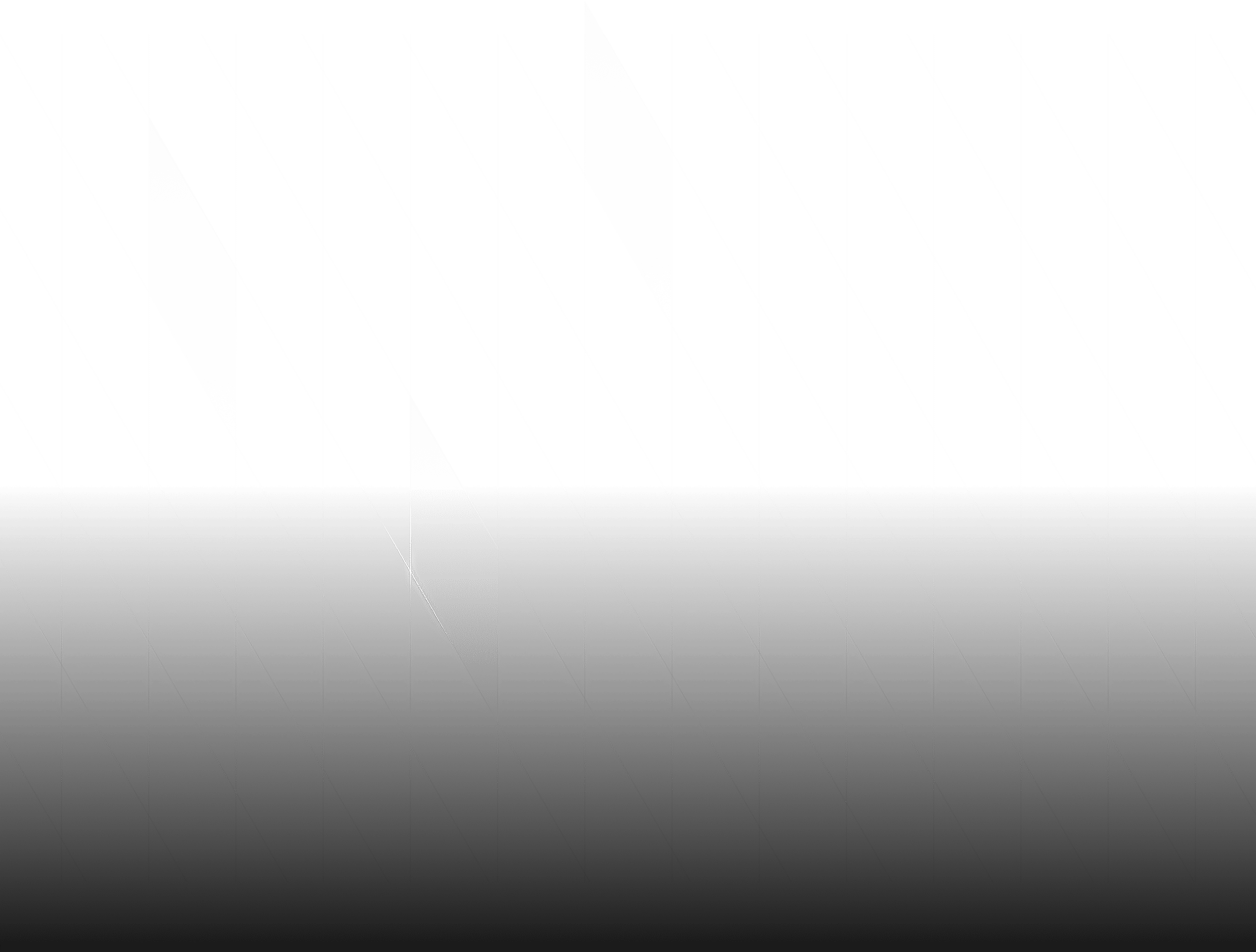
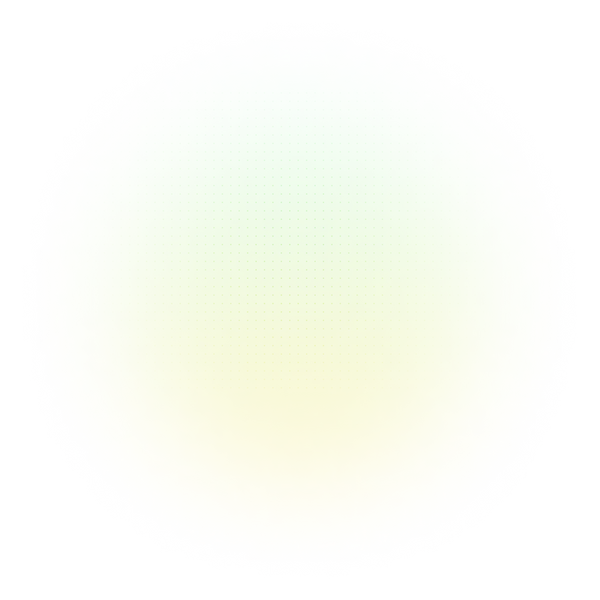

Archer Daniels Midland (ADM), a global agricultural powerhouse with over 40,000 employees and more than 450 locations worldwide, transformed its reliability program by standardizing its Root Cause Analysis (RCA) process with EasyRCA. The results were decisive: over $30 million in cost savings, 700+ RCAs completed, and a cultural shift that improved morale, ownership, and cross-functional collaboration across the company.
The Challenge: Disconnected Tools, Incomplete RCAs, and a Reactive Culture
Before EasyRCA, ADM’s RCA efforts were inconsistent and difficult to scale. With no standard tool in place, teams across business units were using at least six different RCA tools and platforms. Each operated in isolation, making it difficult to track trends, share lessons learned, or close the loop on recurring issues.
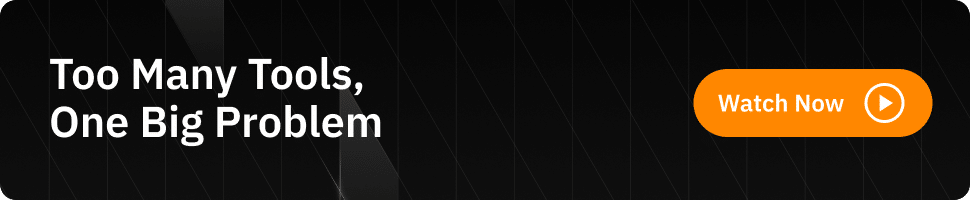
Whiteboard sessions and 5-Why RCAs often stalled before reaching root causes. This led to a pattern of unresolved failures, rising maintenance costs, and a workforce bogged down in reactive tasks. “Morale was low,” said Matt Sadler, Global Reliability Engineer. “People were dealing with the same failures over and over. They were burnt out.”
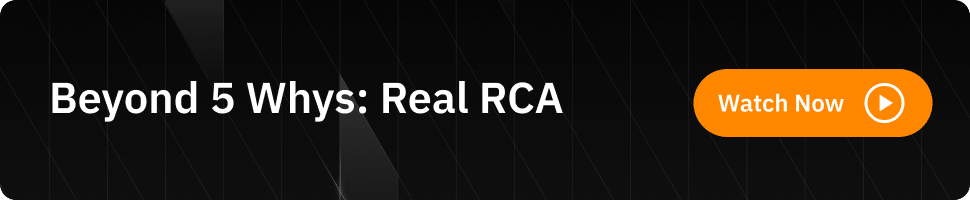
The Turning Point: A Clear Mandate and an Easy-to-Adopt Solution
ADM leadership recognized that a shift was needed—from reactive firefighting to structured problem-solving. The company began searching for a single, accessible RCA platform that could scale across regions, departments, and experience levels.
EasyRCA quickly proved to be that solution.
ADM launched a pilot in 10 plant locations in 2022. The early success—24 RCAs completed and $940K in cost impact—sparked broader interest across the organization. EasyRCA was then rolled out to four major business units, accompanied by training and support to help local teams adopt the platform.
Today, it’s not just the Maintenance and Reliability teams using EasyRCA. It’s also being used by:
- Food Safety and Quality teams
- Environmental Health & Safety (EHS)
- Continuous Improvement and Performance Excellence groups
“Frontline teams grabbed hold of EasyRCA first… and now every function of ADM is using it.” — Matt Sadler
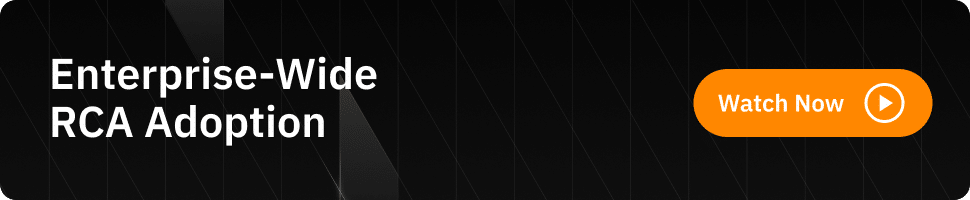
The Impact: $30 Million Saved, Culture Transformed
Financial & Operational Outcomes
ADM has achieved $30 million in documented cost savings by addressing chronic failure patterns and implementing sustainable corrective actions. Those savings include:
- Fewer emergency repairs and reduced overtime
- Increased uptime and throughput in processing and packaging
- Lower replacement part consumption and inventory strain
- More efficient use of skilled labor
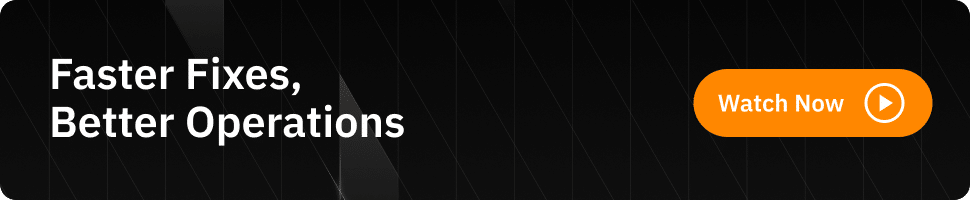
Key reliability metrics improved:
- Mean Time Between Failures (MTBF) increased
- RCA closure rate rose significantly
- PM/CM ratio shifted toward proactive, preventive work
A Cultural Transformation from the Ground Up
While the financial gains were substantial, the shift in workplace culture has been just as meaningful.
EasyRCA helped drive:
- A new mindset of ownership at the plant level
- Cross-functional collaboration, replacing siloed investigations
- Visible improvement in morale: “People are actually excited to come to work,” said Sadler, “because they’re not facing the same emergency failure day in and day out.”
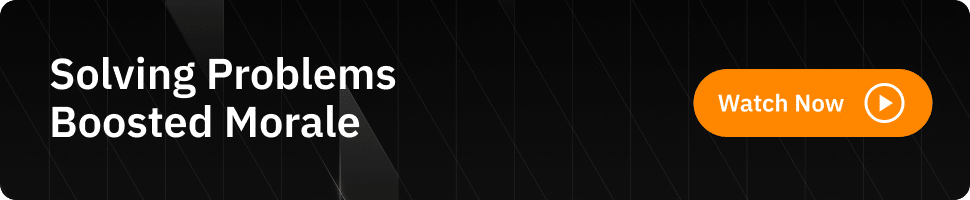
By removing friction from the RCA process and giving everyone—from operators to engineers—a seat at the table, EasyRCA helped ADM move from a blame-oriented environment to a learning-focused culture grounded in data and problem-solving.
“EasyRCA came alongside us… they were partners in this journey. That really helped and solidified the relationship.” — Matt Sadler
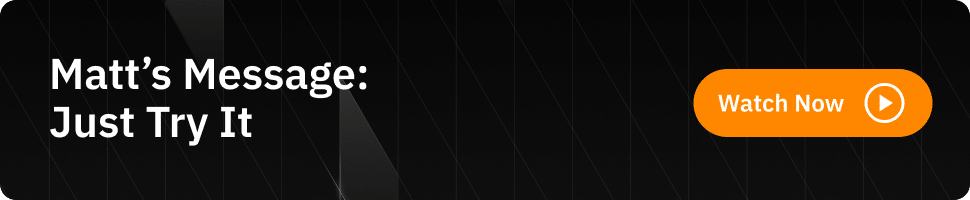
Designed for Everyone, Backed by AI
A key reason for EasyRCA’s rapid adoption was how approachable it is for all experience levels.
“You don’t have to be a practitioner of root cause analysis,” said Sadler. “You can jump in and get to those root causes and put solutions in place much quicker.”
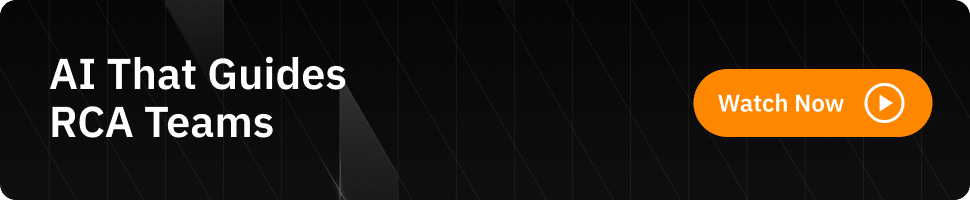
With AI-powered guidance, the platform helps even junior facilitators go deeper and gain confidence. It also supports consistency across teams—ensuring each RCA is thorough, well-documented, and actionable.
What’s Next for ADM
ADM plans to continue expanding EasyRCA across more sites and assets, making it a cornerstone of their long-term reliability and continuous improvement strategy.
“We didn’t force it,” said Sadler. “We said: try it. If you like it, adopt it. That approach, along with EasyRCA’s support, made all the difference.”
See the Impact for Yourself
If your organization is battling repeat failures, disconnected RCA efforts, or reactive maintenance, EasyRCA can help you make the same shift ADM did—one that unlocks real savings and builds lasting reliability.
Book a demo or explore training options to start your journey.
Ignite your curiosity, subscribe now!
Stay informed and connected with the latest updates by subscribing today!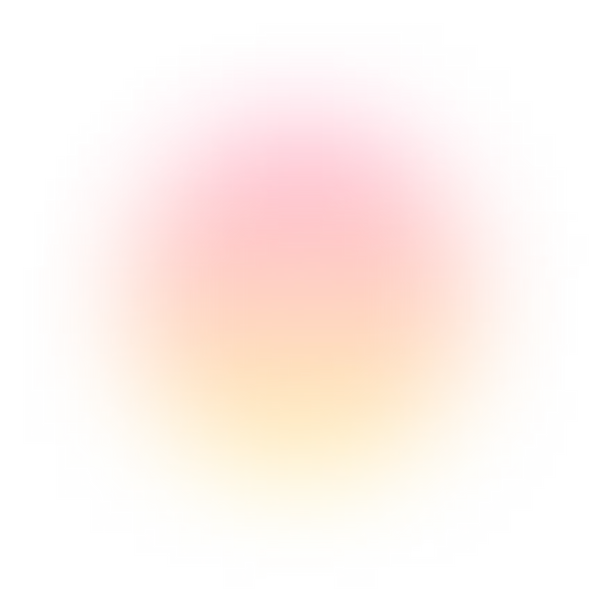
Recent Comments