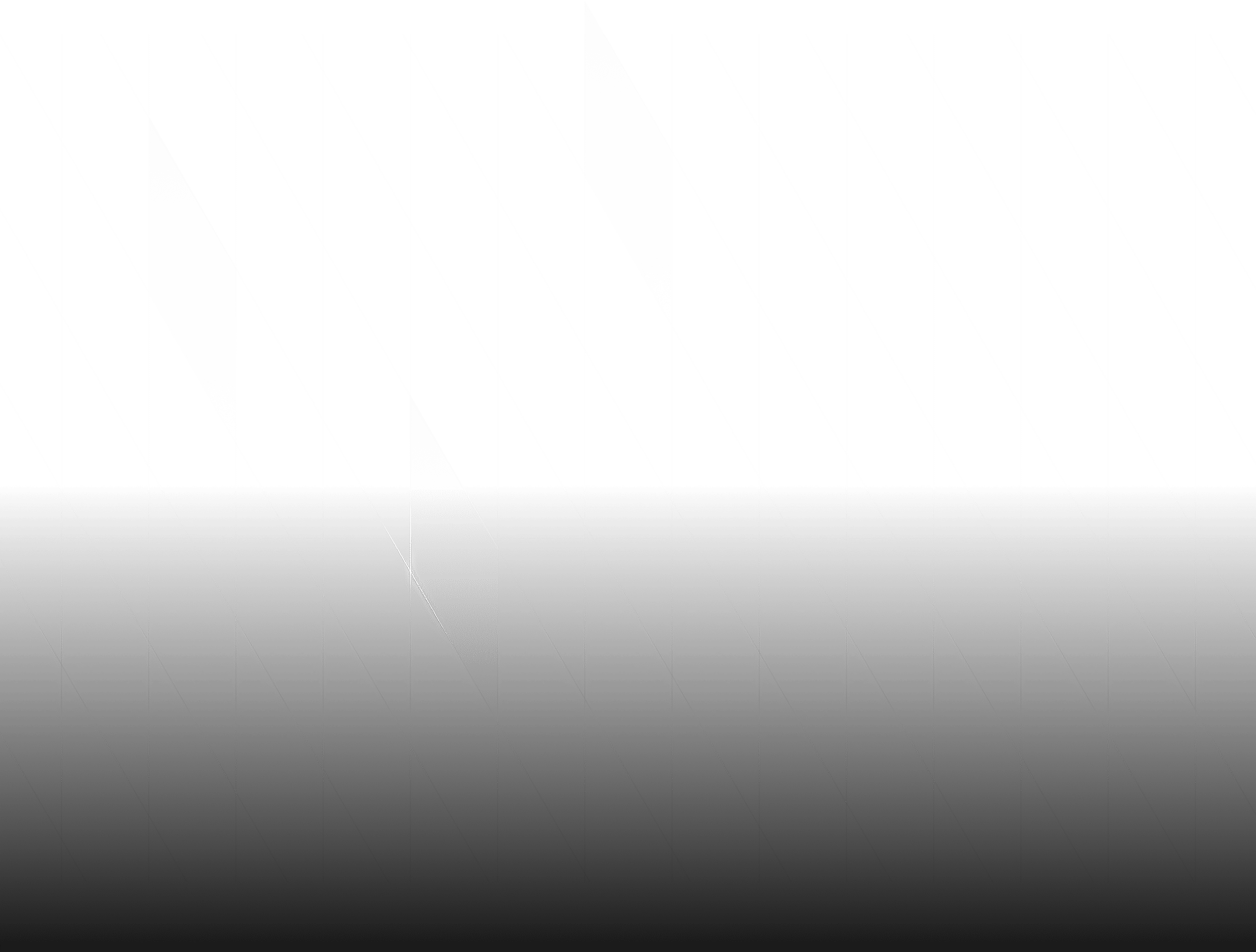
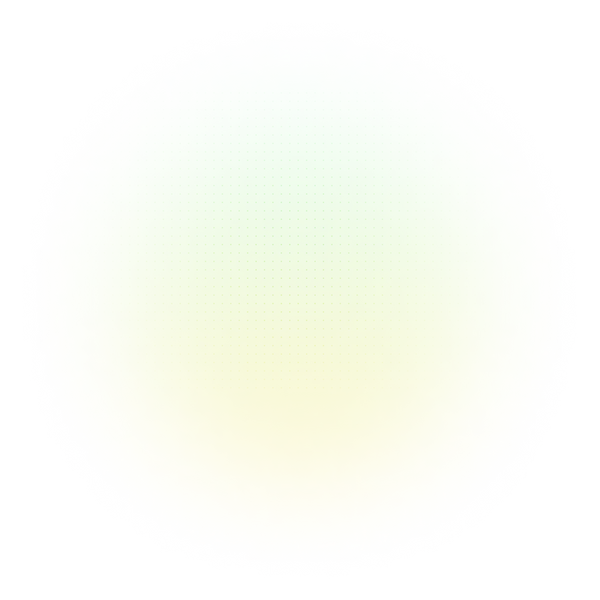

“So far, we have more than 140 RCAs in the system… and we’ve seen a reduction in unplanned downtime.” – Edwin Gutierrez, Corporate Reliability Engineer, Ash Grove Cement
In under a year, Ash Grove Cement rolled out EasyRCA across 12 plants, trained cross-functional teams, and built a culture of root cause accountability—with over 140 investigations and measurably reducing unplanned downtime.
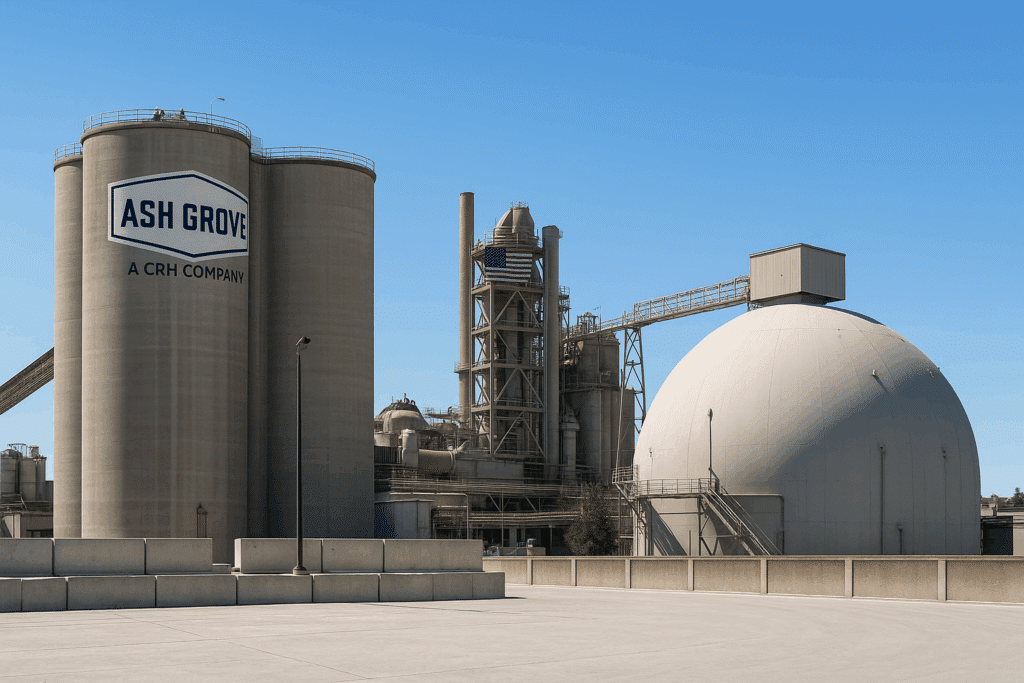
Table of Contents
- Quick Results: RCA Volume and Downtime Reduction
- The Challenge: RCA Processes That Didn’t Deliver
- The Solution: Bringing EasyRCA to Ash Grove
- Implementation: Training, Coaching, and Adoption
- Key Features That Made the Difference
- Real Use Cases: From Kilns to Safety Incidents
- Advice for Others: Build Your Facilitators
- Conclusion: Reliability as a Team Effort
Quick Results: RCA Volume and Downtime Reduction
Ash Grove Cement saw measurable success after implementing EasyRCA:
- ✅ 140+ RCAs completed in less than 10 months
- ✅ Reduction in unplanned downtime across plants
- ✅ Action tracking embedded in the workflow, increasing accountability
- ✅ Improved collaboration between teams, including maintenance, safety, and process engineering
“We didn’t have that scale before. Now we can track every action, every RCA—and even celebrate when plants perform well.”
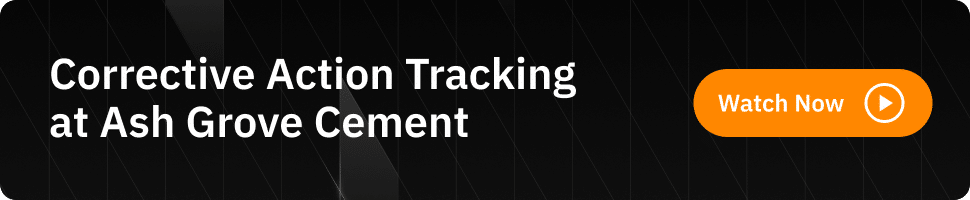
The Challenge: RCA Processes That Didn’t Deliver
When Edwin joined Ash Grove as Corporate Reliability Engineer, he audited the company’s RCA efforts. The results were clear:
“Nobody was able to complete a root cause analysis. The software wasn’t designed for it—it was more of a CMMS concept.”
The CMMS RCA module lacked structure, transparency, and follow-through. Investigations stalled. Critical issues went unresolved. The organization needed a purpose-built solution.
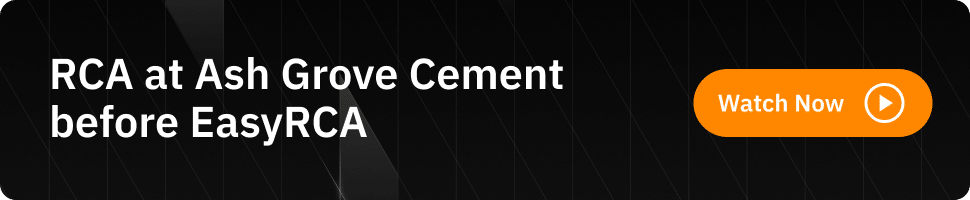
The Solution: Bringing EasyRCA to Ash Grove
Edwin introduced EasyRCA to give teams the clarity and structure they needed.
“EasyRCA is a web application. We can track actions, track RCA completion, and share everything across the company.”
Because Edwin had used EasyRCA successfully in a previous role, he was confident it would deliver results. The company adopted the platform and began to implement it across its 12 locations.
Implementation: Training, Coaching, and Adoption
Edwin built a training program, conducted on-site sessions, and personally coached engineers on the software and methodology.
“The best way to build relationships on-site is to teach. I’m coaching younger engineers now—they’re developing into RCA facilitators.”
He emphasized not only technical proficiency but also soft skills: diplomacy, communication, and methodological rigor.
“Being an RCA facilitator isn’t just about technical skills. You need to manage the room and respect the process.”
Key Features That Made the Difference
Ash Grove found significant value in EasyRCA’s feature set:
- Action Center: “We can see how many actions are pending—per plant or per RCA owner. People even get email reminders.”
- Cross-functional Access: “Everyone in the plant can see the dashboard—even management. That creates positive pressure.”
- Accountability with Recognition: “When we see plants performing well, we congratulate them. It’s not just pressure—it’s recognition.”
- AI Tools: “Now, I don’t have to go to a book. The book is already in the software.”
The AI assistant helped teams accelerate their investigations—while Edwin emphasized the need to validate and document findings properly.
The AI assistant helped teams accelerate their investigations—while Edwin emphasized the need to validate and document findings properly.
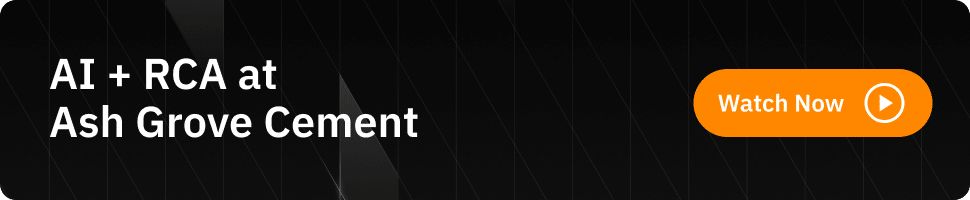
Real Use Cases: From Kilns to Safety Incidents
Ash Grove focuses its RCAs on the most critical equipment at each site—like kilns, finish mills, or key process systems.
“We’re tracking those equipment failures and analyzing them based on corporate triggers. Some plants have their own triggers, but we’re standardizing.”
They’re also using EasyRCA outside of maintenance:
“We’ve used the software for safety incidents. And for quality—because if we lose quality, we lose market.”
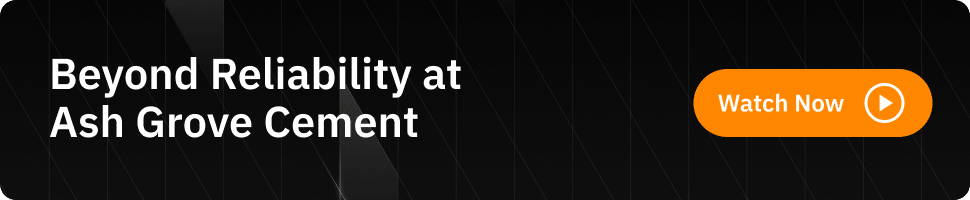
Advice for Others: Build Your Facilitators
Edwin’s advice to organizations considering EasyRCA?
“Train your people. Prepare your RCA facilitators. If you do it the right way, you’ll get amazing results.”
He emphasized that great facilitators combine technical ability with leadership and communication skills.
“You have to be diplomatic—but also tough about respecting the methodology.”
Conclusion: Reliability as a Team Effort
With EasyRCA, Ash Grove Cement created more than a database of RCAs—they built a reliability culture.
“Now we’re aiming to improve reliability and reduce the number of failures.”
The shift is visible, measurable, and company-wide. RCA is no longer a siloed task—it’s a shared discipline backed by a reliable system, a trained team, and leadership that celebrates success.
Want to improve your RCA performance like Ash Grove?
👉 Book a demo or explore training options to start your journey.
Watch or listen to our full podcast interview with Edwin Gutierrez, Corporate Reliability Engineer at Ash Grove Cement.
Photo Credit: Joe Mabel
Ignite your curiosity, subscribe now!
Stay informed and connected with the latest updates by subscribing today!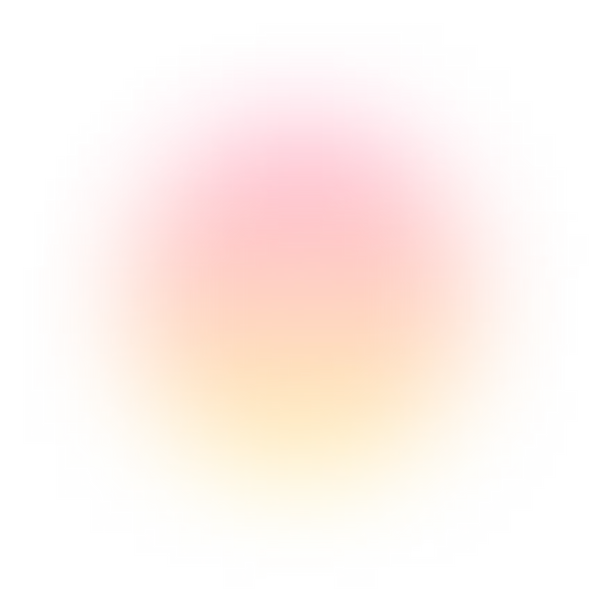
Recent Comments