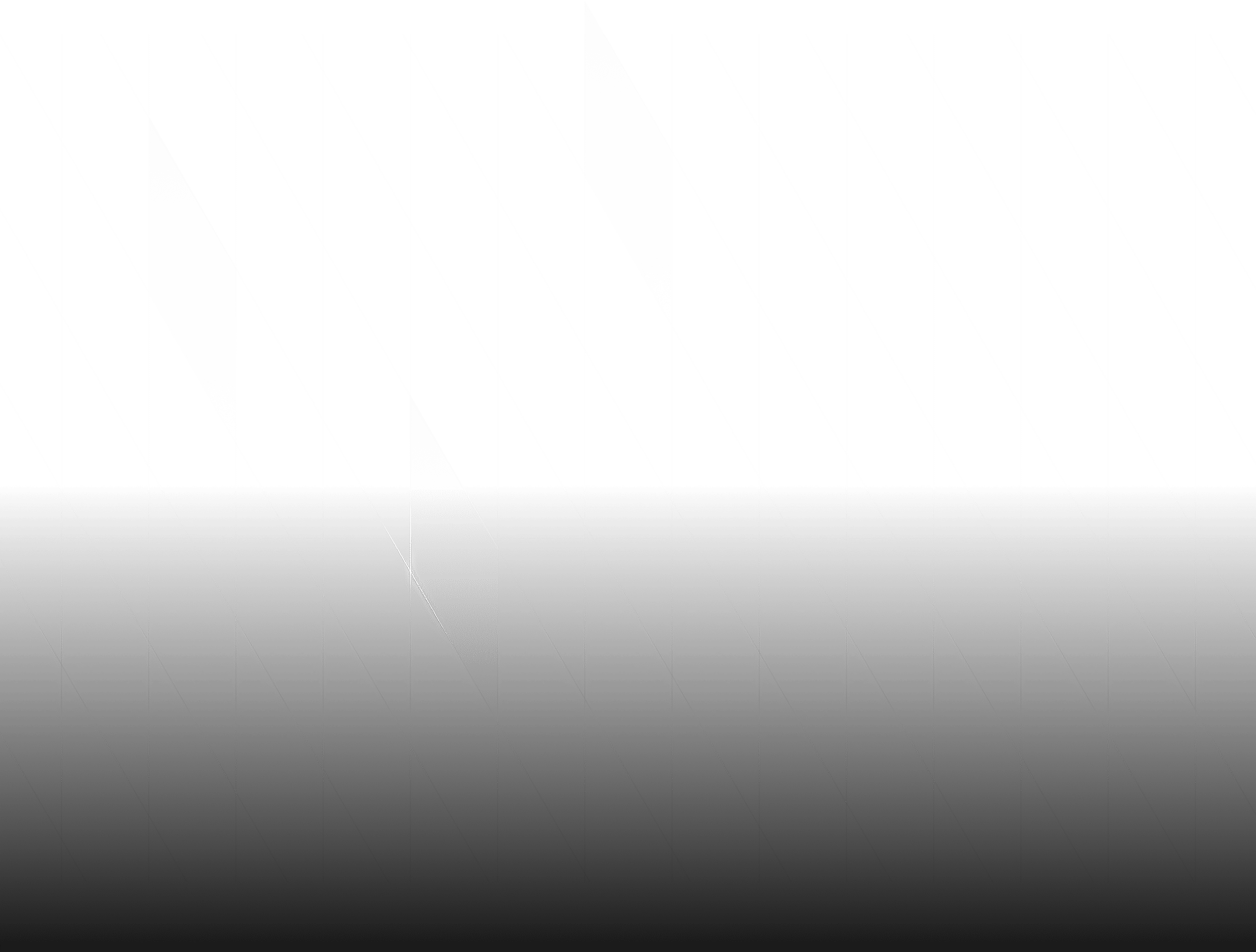
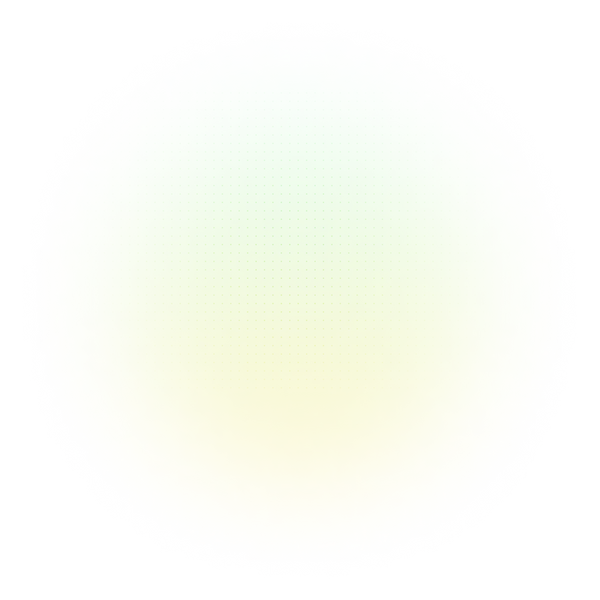

With over two decades in business – spanning strategy consulting, tech startups, and executive leadership – I am committed to helping your organization thrive.
At Reliability, we’re on a mission to help enhance strategic decision-making and operational excellence through the power of Root Cause Analysis, and I hope this article will be helpful!
We aim to help you better understand real-life case studies of reliability improvement by offering insights, case studies, and practical tips based on years of experience. Whether you’re new to doing root cause analyses or a seasoned pro, we trust this will be useful in your journey towards working hard and working smart.
The Challenge: A Fragmented Approach to RCA
Archer-Daniels-Midland (ADM) is a global leader in agricultural processing which operates across 450 facilities worldwide. Managing reliability for such a vast network comes with unique challenges. ADM’s global reliability engineer, Matt Sadler, described a key challenge: “We were using six different versions of root cause analysis tools. That made it difficult to pull data from a central source, and decisions often relied on incomplete information”.
This left ADM needing help standardizing RCAs across its plants, making it harder to identify systemic issues and derive actionable insights. The lack of a clear plan affected operational efficiency and frustrated many employees with recurring problems.
The Solution: EasyRCA Unifies and Simplifies
To address these challenges, ADM started to use EasyRCA—a user-friendly RCA platform designed to streamline processes. EasyRCA stood out because it enables users to concentrate on identifying the root cause and swiftly implementing solutions.
One of the software’s standout features was its accessibility, as it catered to employees with varying levels of experience, from new graduates to seasoned professionals. EasyRCA’s straightforward interface enabled everyone to easily get started and solve problems effectively.
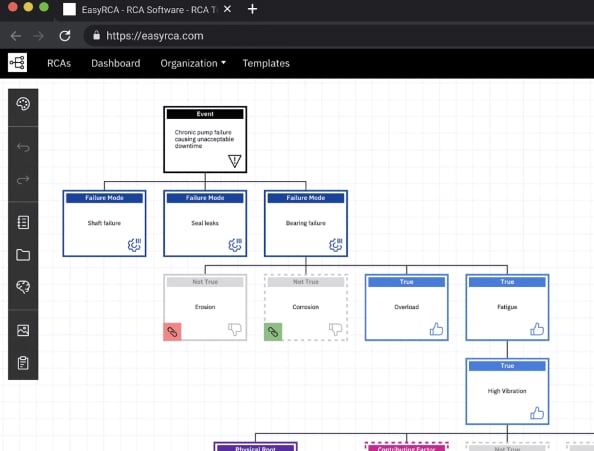
The Implementation: Gaining Traction Across Departments
ADM initially rolled out EasyRCA within its Maintenance and Reliability team, utilizing it for tasks like bad actor analysis and failure mode identification. The tool’s immediate impact spurred other departments to start using the platform as well, including Food Safety, Environmental Health, and Continuous Improvement.
ADM’s leadership encouraged plant teams to try the software without mandating its use. This flexibility helped gain buy-in from employees. “We didn’t force it on any plant locations,” Matt explained. “We simply said, ‘Try it. If you like it, adopt it, and we’ll support you.’ That approach really resonated with our teams.”
Results: Operational Efficiency and Morale Boost
The integration of EasyRCA quickly delivered measurable results:
- Improved Efficiency: Standardized RCA methods enabled ADM to identify and resolve systemic issues, particularly in processing and packaging lines. Matt noted a significant increase in throughput and efficiencies across the network.
- Enhanced Morale: Employees experienced noticeable improvements as systemic problems diminished. According to Matt, this shift reduced the frequency of emergency failures, making work more enjoyable and boosting morale.
- Data-Driven Decisions: By consolidating RCA data into a single platform, ADM’s leadership gained clearer insights into performance and risks, enabling more informed decision-making.
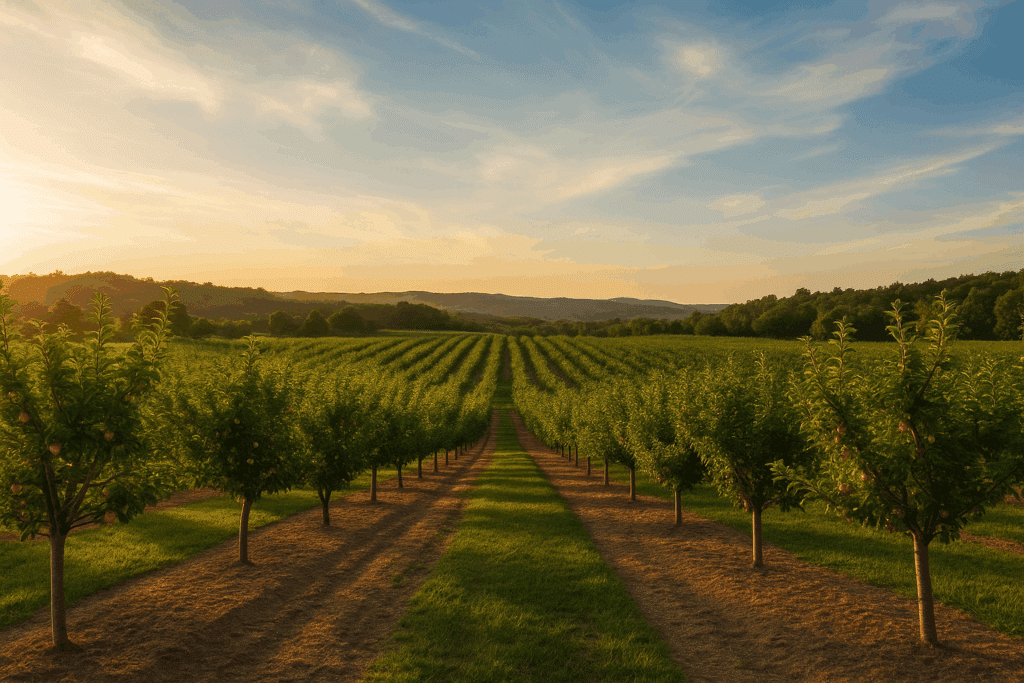
Looking Ahead: Enhancing RCA with AI and Analytics
ADM plans to expand its use of EasyRCA with AI tools to assist junior facilitators. They also plan to enhance reporting capabilities to reflect the wider impact of RCAs, going beyond cost savings to include improvements in safety, environmental compliance, and employee engagement.
Final Thoughts: A Practical Tool for Real Results
For ADM, adopting EasyRCA was not just a technological upgrade; it signified a major cultural shift. Matt noted that “EasyRCA became the norm, not just the ‘next shiny thing’”. The software’s practicality and accessibility made it a trusted tool across departments, empowering employees to solve problems and drive meaningful change.
ADM’s story underscores the value of selecting tools that align with your organization’s needs and processes. To learn more about how EasyRCA can support your reliability goals, explore our resources or schedule a live demo.
Watch Matt Sadler’s insights directly on our podcast.
I hope you found this case study insightful and actionable! Stay tuned for more thought-provoking articles as we continue to share our knowledge. Success is rooted in a thorough understanding and consistent application, and we hope this article was a step in unlocking the full potential of Root Cause Analysis for your organization.
Reliability runs initiatives such as an online learning center focused on the proprietary PROACT® RCA methodology and EasyRCA.com software. For additional resources, visit EasyRCA Resources.
Ignite your curiosity, subscribe now!
Stay informed and connected with the latest updates by subscribing today!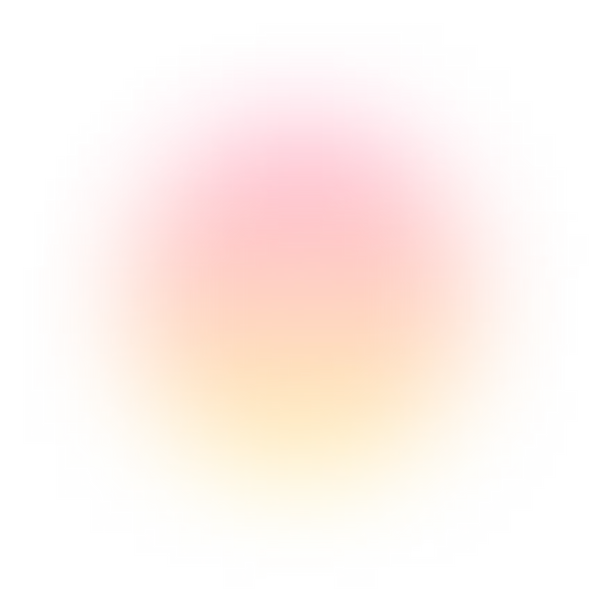
Recent Comments