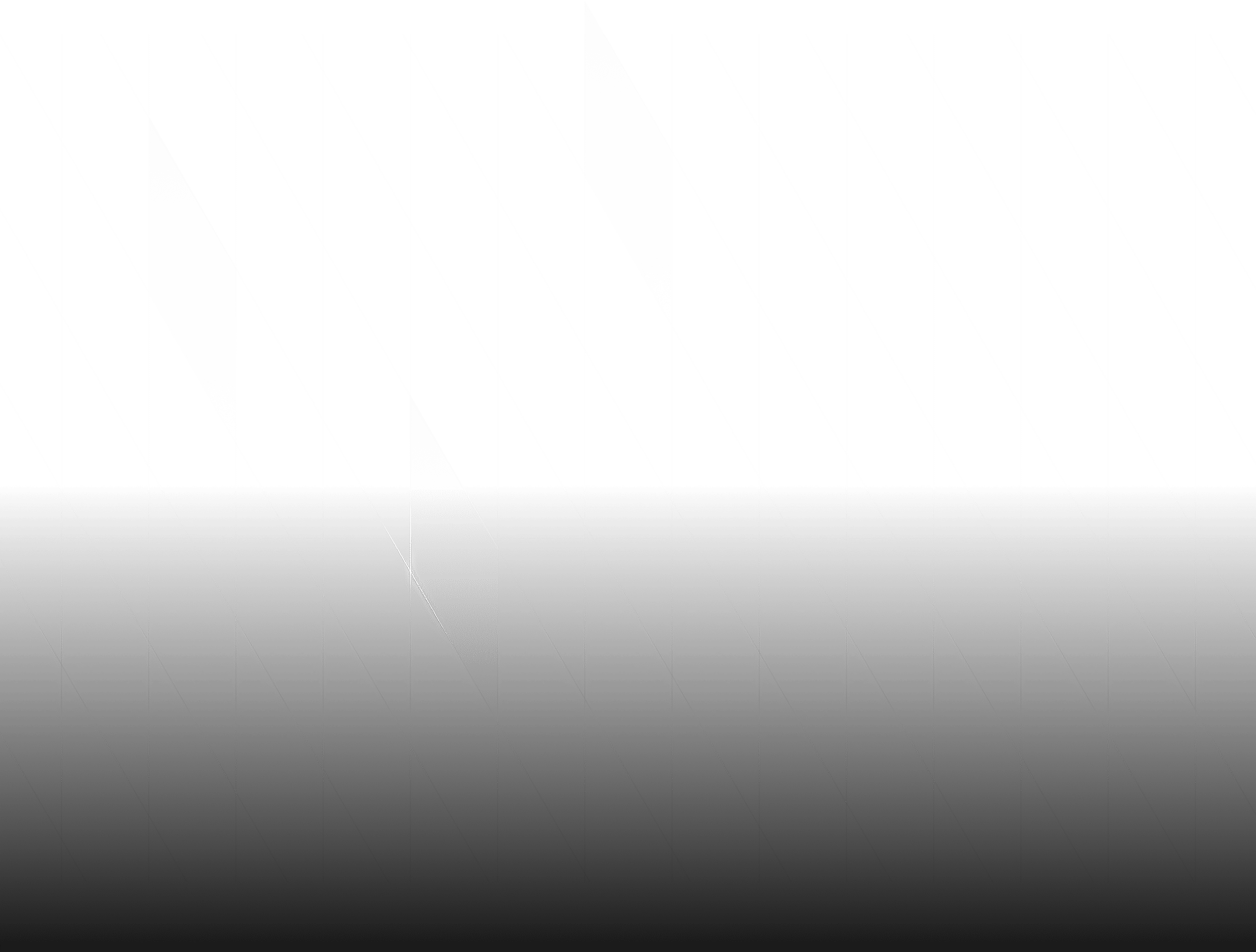
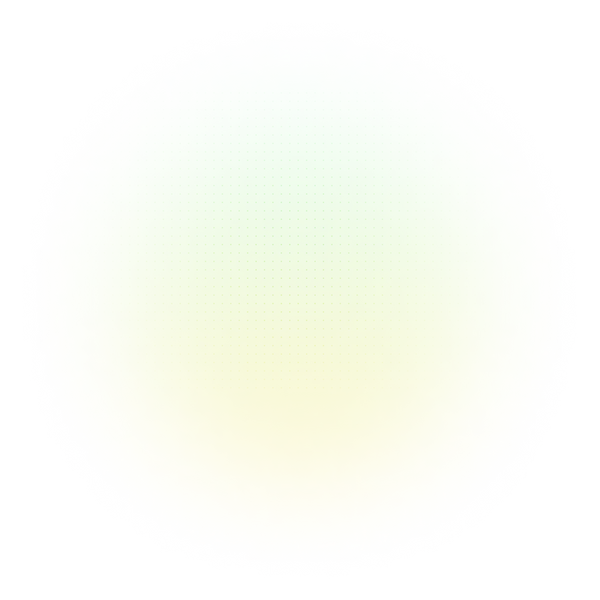

With over two decades in business – spanning strategy consulting, tech startups, and executive leadership – I am committed to helping your organization thrive.
At Reliability, we’re on a mission to help enhance strategic decision-making and operational excellence through the power of Root Cause Analysis, and I hope this article will be helpful!
Our goal is to help you better understand root cause analysis by offering insights and practical tips based on years of experience. Whether you’re new to doing RCAs or a seasoned pro, we trust this will be useful in your journey towards working hard and working smart.
———————
When we encounter a problem, it’s natural to address the immediate issues at hand. However, Root Cause Analysis delves deeper into the underlying reasons for these problems, aiming to identify and resolve the fundamental issues that lead to specific outcomes.
Root cause analysis is a systematic method of problem-solving used to identify the underlying causes of issues or events. It involves digging beneath the surface to uncover the primary factors that contribute to a particular problem. By understanding these foundational causes, we can develop more effective solutions and prevent similar issues from arising in the future.
Why Do We Even Bother?
The significance of conducting root cause analysis extends beyond just addressing immediate concerns. By identifying and addressing the root cause of a problem, we can prevent its recurrence, leading to long-term improvements in processes and outcomes. This approach not only saves time and resources but also enhances overall efficiency and effectiveness.
Followings are four different types of root cause analysis to help us uncover the root causes of a problem.
The Classic 5 Whys Method

When it comes to root cause analysis, the 5 Whys method is a powerful tool for uncovering the underlying reasons behind a problem.
Understanding the 5 Whys
The 5 Whys technique involves asking “why” multiple times to drill down to the core issue. By repeatedly questioning the initial response, we can reveal deeper layers of causation until we reach the fundamental reason behind a problem. Here’s a simple breakdown of how it works:
- Ask Why: Start by identifying the problem and ask why it occurred.
- Repeat: For each answer generated, ask why again to delve further into the issue.
- Continue: Repeat this process five times or until reaching a point where additional “whys” no longer provide meaningful insights.
This method helps in identifying not just the immediate cause of an issue, but also its underlying factors, ultimately leading to a more comprehensive understanding of the problem.
When to Use the 5 Whys
Example: Solving a project issue
Imagine encountering difficulties with completing a project on time. Applying the 5 Whys method can be incredibly insightful in this scenario:
- First Why: The project was delayed because there wasn’t enough time to finish it.
- Second Why: Why wasn’t there enough time? Because another project took precedence.
- Third Why: Why did the other project take precedence? Because they were equally important and had similar deadlines.
- Fourth Why: Why were multiple important projects scheduled simultaneously? Because of poor time management and planning.
- Fifth Why: Why was there poor time management and planning? Because of underestimating the workload and not prioritizing effectively.
By asking these iterative “whys,” we uncover that the root cause lies in inadequate time management and prioritization skills rather than simply running out of time. This realization allows for targeted solutions that address these fundamental issues.
The Detailed Fishbone Diagram
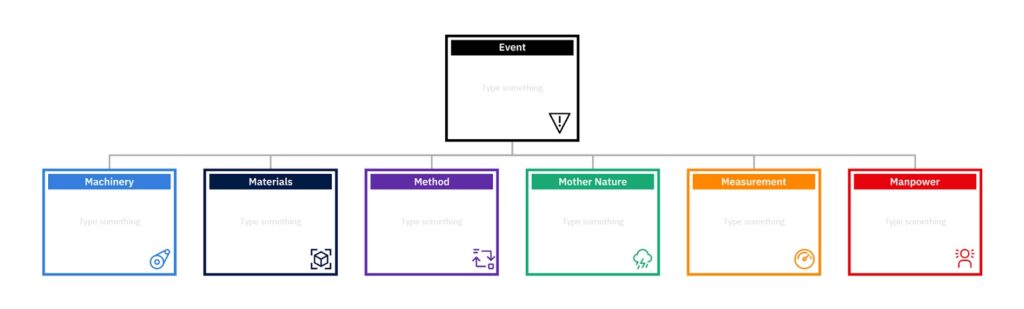
Moving on from the 5 Whys method, another valuable tool for root cause analysis is the Fishbone Diagram. This visual representation, also known as the Ishikawa diagram, helps to systematically identify potential causes of a specific issue.
What’s a Fishbone Diagram?
The Fishbone Diagram is structured like a fish’s skeleton, with the “head” representing the problem or effect, and the “bones” branching out to various categories of potential causes. These categories typically include manpower, methods, materials, machinery, measurement, and environment. Each category serves as a starting point for identifying factors that could contribute to the problem at hand.
Fishbone Diagram in Action
Example: Identifying reasons for late project submissions
Let’s consider an example where staff consistently submit their projects after the due date. By using a Fishbone Diagram, we can analyze potential causes:
- Manpower: Are there enough assistants to provide support and clarify doubts?
- Methods: Is there a standardized process for submitting projects? Are staff aware of it?
- Materials: Do staff have access to the necessary resources and materials to complete their projects?
- Machinery: In this context, machinery could refer to technological tools such as online platforms for project submission.
- Measurement: How are deadlines communicated and enforced? Is there clarity on expectations?
- Environment: Does the learning environment support the effective completion of projects?
By exploring each category in detail, we can uncover underlying issues contributing to late submissions. For instance, inadequate access to necessary materials or unclear communication about deadlines could be significant factors.
Utilizing a Fishbone Diagram provides a comprehensive view of potential causes, enabling educators to address fundamental issues that impact student performance.
PROACT® Methods
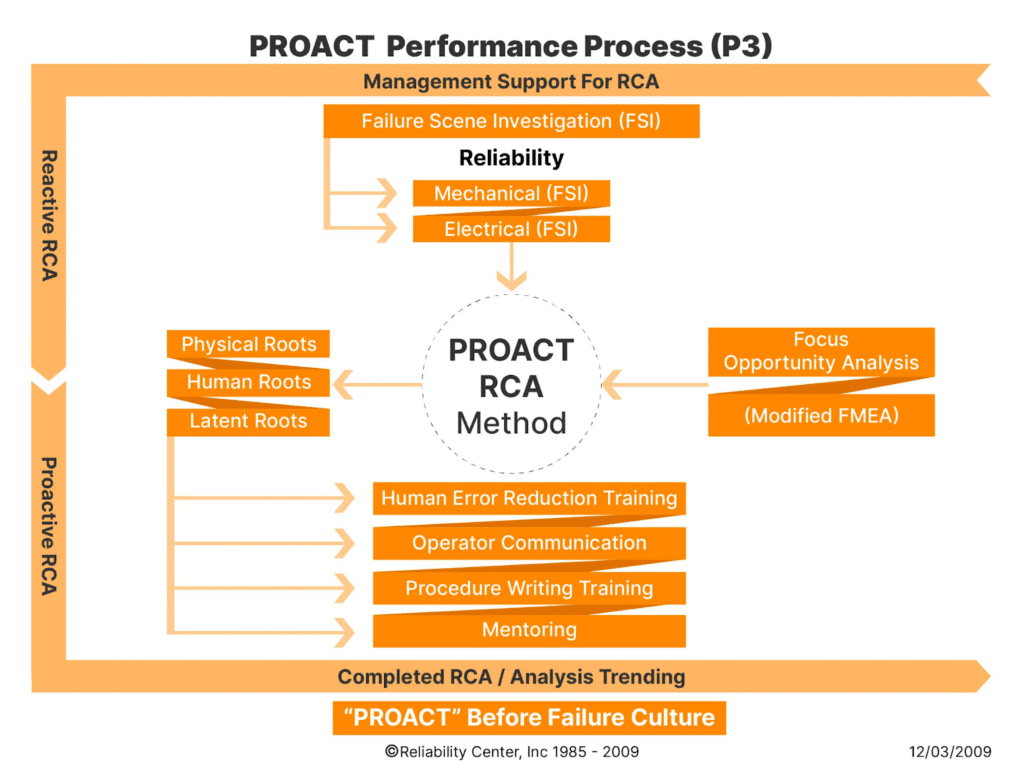
Now, let’s delve into another effective approach for root cause analysis known as the PROACT® Method. The PROACT® acronym stands for the following basic, investigative process steps:
- PReserving Evidence and Acquiring Data
- Order Your Analysis Team and Assign Resources
- Analyze the Event
- Communicate Findings and Recommendations
- Track and Measure Impact for Bottom Line Results
Applying the PROACT® Method
The PROACT® method is applied through a systematic approach to root cause analysis, focusing on three key areas: the root system, the analysis, and the knowledge base.
Identifying Root Causes:
Begin by thoroughly examining the physical, human, and latent root causes contributing to the problem.
- Physical Root Causes: Direct consequences of decision-making or tangible components that lead to failures or breakdowns in the system.
- Human Root Causes: Decision errors or actions (or inactions) that trigger physical root causes, often influenced by organizational culture or individual behavior.
- Latent Root Causes: Cultural barriers, perceived flaws in organizational systems, or support systems affecting behavior and decision-making.
Conducting Root Cause Analysis:
In applying the PROACT® method, it’s essential to analyze how root causes interact to contribute to the problem, tracing the sequence from human decisions to physical consequences. Additionally, examine how latent factors in organizational culture or systems influence decision-making. This analysis provides insights into the underlying causes, aiding in the development of effective prevention strategies.
Leveraging Organizational Knowledge:
By leveraging the organization’s collective knowledge and experience, potential root causes can be identified and effective solutions developed. Sharing insights from past experiences, including both failures and successes, informs decision-making and enhances future outcomes. Ongoing training and support are provided to enhance problem-solving capabilities and ensure all staff possess the necessary skills and knowledge. Through the application of the PROACT® method, organizations can proactively identify and address the root causes of problems, facilitating more effective solutions and continuous improvement in reliability and maintenance management.
Fault Tree Analysis (FTA)
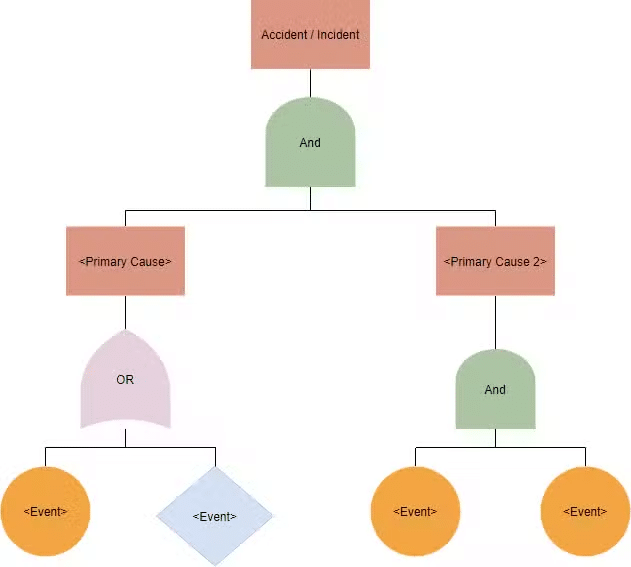
Now, let’s explore another valuable method for root cause analysis known as Fault Tree Analysis (FTA). This approach provides a structured way to identify potential causes of a specific event or problem by mapping out the various contributing factors.
Understanding Fault Tree Analysis
Fault Tree Analysis is a systematic and visual approach used to identify how specific events or failures can occur. It involves constructing a graphical representation of all potential combinations of factors that could lead to the occurrence of an undesired event. By examining these combinations, organizations can gain insights into the critical factors contributing to an issue.
Steps in Fault Tree Analysis (FTA)
Breakdown of the FTA process
The process of conducting Fault Tree Analysis involves several key steps:
- Identify the Undesired Event: Begin by clearly defining the undesired event or outcome that requires analysis. This could be a safety incident, equipment failure, or any other adverse occurrence.
- Identify Basic Causes: Identify and list down all the basic causes that could contribute to the undesired event. These causes serve as the building blocks for constructing the fault tree.
- Constructing the Fault Tree: Create a visual representation where the top event (undesired outcome) is placed at the top of the tree, with various intermediate events and basic causes branching out below it. The relationships between these events are depicted using logical gates such as AND, OR, and NOT gates.
- Analysis and Evaluation: Once the fault tree is constructed, analyze it to determine all possible combinations of basic causes that could lead to the top event. Evaluate each combination to understand their significance in causing the undesired outcome.
- Identifying Critical Paths: Identify critical paths within the fault tree, which represent specific combinations of basic causes that directly lead to the top event. These critical paths highlight key areas where preventive measures should be focused.
By following these steps, organizations can systematically analyze potential causes and pathways leading to undesired events, enabling them to prioritize preventive actions effectively.
Application of Fault Tree Analysis
Let’s consider a real-life example where Fault Tree Analysis is applied to identify potential causes behind a manufacturing equipment failure:
- Undesired Event: Production line shutdown due to equipment failure.
- Basic Causes Identified: Lack of regular maintenance, wear and tear due to prolonged usage, and inadequate training for equipment operators.
- Constructing the Fault Tree: A fault tree is created with logical connections between these basic causes and their potential impact on equipment failure.
- Analysis and Evaluation: The fault tree is analyzed thoroughly to understand how different combinations of basic causes could lead to equipment failure.
- Identifying Critical Paths: Critical paths are identified within the fault tree, highlighting specific combinations such as lack of maintenance coupled with prolonged usage that directly contribute to equipment failure.
Through this analysis, it becomes evident that addressing both regular maintenance practices and providing comprehensive training for equipment operators is crucial in preventing production line shutdowns due to equipment failures.
By utilizing Fault Tree Analysis in this scenario, organizations can gain valuable insights into critical factors contributing to operational disruptions and take targeted actions toward preventing such occurrences in the future.
Tips for picking a method based on your situation
- Nature of the Problem: Evaluate the nature and complexity of the problem at hand. For simpler issues with clear cause-and-effect relationships, methods like the 5 Whys or Fishbone Diagram may suffice. However, complex and multifaceted problems may require more detailed approaches such as Fault Tree Analysis or PROACT® RCA.
- Available Data and Resources: Consider the availability of data and resources for conducting the analysis. Some methods may require extensive data collection and analysis, while others can be implemented with limited resources. Choose a method that aligns with the available information and expertise within your organization.
- Time Sensitivity: Assess the urgency of addressing the problem. If immediate action is required, methods that allow for quick identification of root causes, such as the 5 Whys, may be preferable. For long-term strategic planning, comprehensive methods like Fault Tree Analysis or PROACT® RCA could be more suitable.
- Organizational Culture: Take into account the organizational culture and familiarity with different root cause analysis methods. Methods that align with existing problem-solving practices and are well-understood by team members may facilitate smoother implementation and acceptance.
By fostering a culture of continuous learning, organizations can elevate their ability to identify underlying causes effectively, leading to sustainable solutions that drive ongoing success.
__________
I hope you found this guide to different types of RCA insightful and actionable! Stay tuned for more thought-provoking articles as we continue to share our knowledge. Success is rooted in a thorough understanding and consistent application, and we hope this article was a step in unlocking the full potential of Root Cause Analysis for your organization.
Reliability runs initiatives such as an online learning center focused on the proprietary PROACT® RCA methodology and EasyRCA.com software. For additional resources, visit EasyRCA Resources.
Ignite your curiosity, subscribe now!
Stay informed and connected with the latest updates by subscribing today!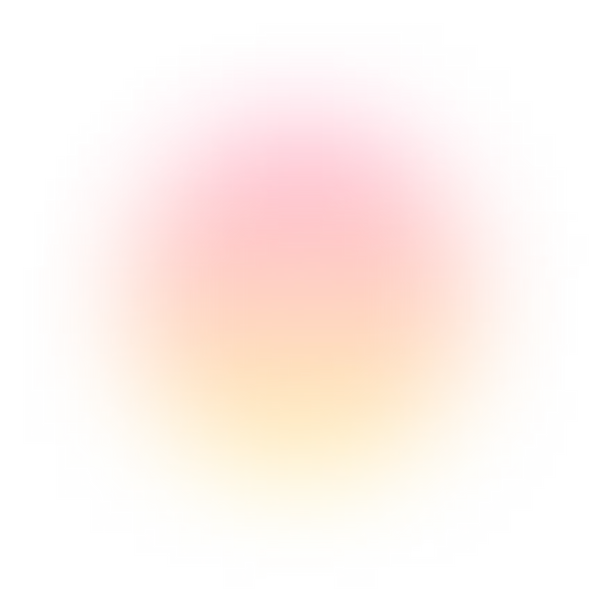
Recent Comments