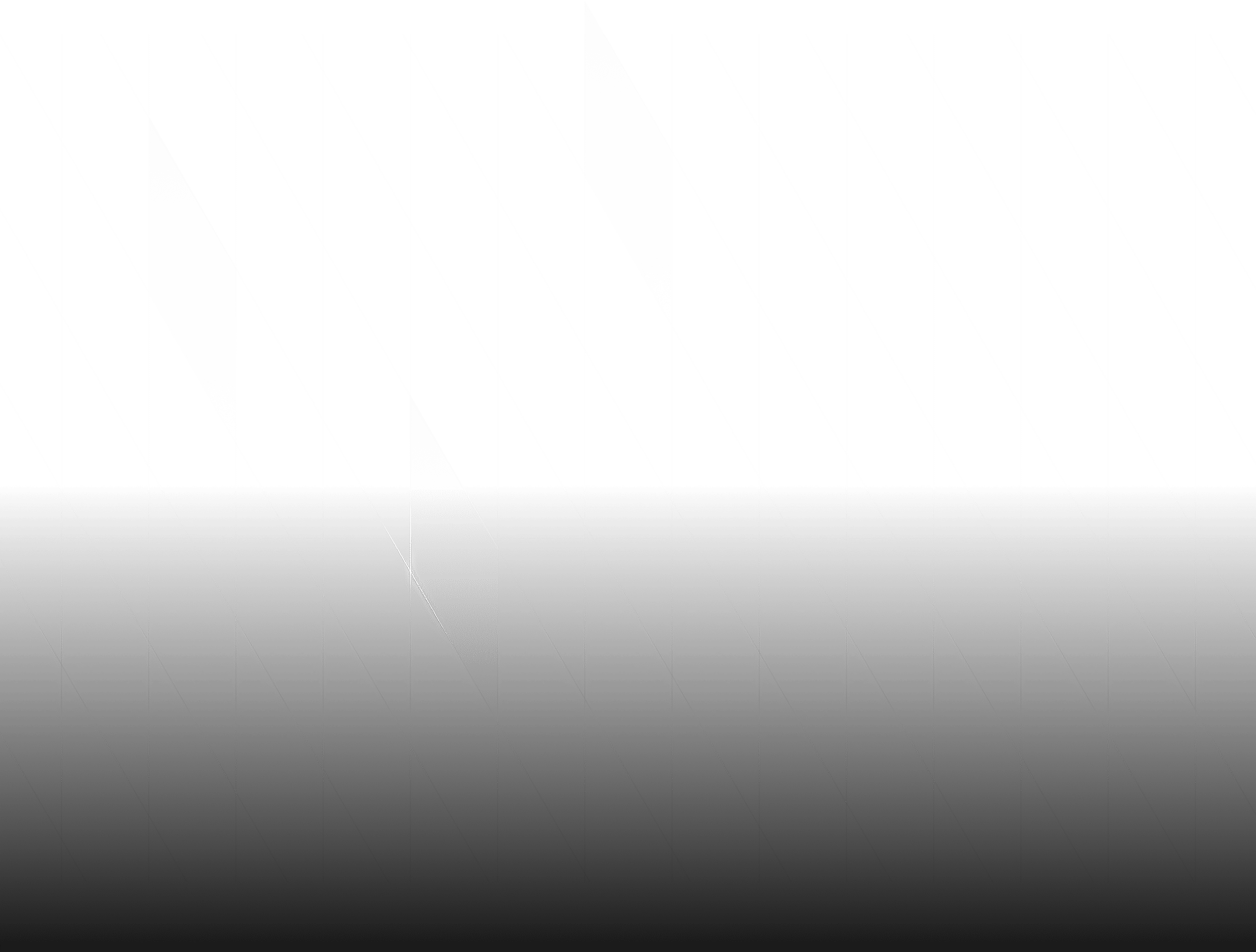
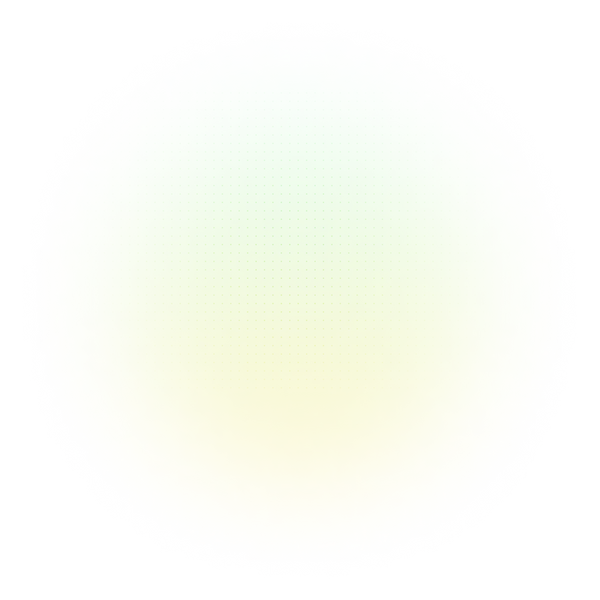

With over two decades in business – spanning strategy consulting, tech startups, and executive leadership – I am committed to helping your organization thrive.
At Reliability, we’re on a mission to help enhance strategic decision-making and operational excellence through the power of Root Cause Analysis, and I hope this article will be helpful!
Our goal is to help you better understand root cause analysis by offering insights and practical tips based on years of experience. Whether you’re new to doing RCAs or a seasoned pro, we trust this will be useful in your journey towards working hard and working smart.
———————
The 5 Whys Technique is a problem-solving method that aims to get to the root cause of an issue by asking “why” multiple times. This technique is based on the simple concept of repeatedly asking “why” to delve deeper into the underlying reasons behind a problem.
The basic concept of the 5 Whys Technique involves identifying a problem and asking “why” it occurred. After each answer, another “why” is asked based on the previous response. This process continues for about five iterations, although it can be more or less depending on the situation. In this article, we have covered how to conduct 5 Why in root cause analysis setting.
How Does 5 Whys Work?
The 5 Whys Technique works by peeling back layers of symptoms to reveal the core issue causing them. By doing so, it helps in understanding the cause-and-effect relationships that contribute to a problem.
The Ideal Situations for Applying the 5 Whys Technique
The 5 Whys Technique is a versatile problem-solving approach that can be applied to various scenarios, both in business and personal development. Understanding the ideal situations for using this technique can help individuals and organizations effectively uncover the root causes of their challenges.
Problem-Solving in Business
In a business setting, the 5 Whys Technique can be instrumental in enhancing quality control and streamlining operations. When faced with recurring issues or unexpected setbacks, organizations can use this method to dig deeper into the underlying reasons behind these problems.
Enhancing Quality Control
By employing the 5 Whys Technique, businesses can gain valuable insights into quality control issues. Whether it’s product defects, customer complaints, or process inefficiencies, asking “why” repeatedly can reveal fundamental flaws in the production or service delivery processes.
Streamlining Operations
Efficient operations are crucial for the success of any business. The 5 Whys Technique can aid in identifying bottlenecks, delays, or errors within operational workflows. By systematically questioning the causes of these issues, organizations can pinpoint areas for improvement and implement targeted solutions.
Personal Growth and Development
Beyond the corporate environment, individuals can also leverage the 5 Whys Technique to navigate personal obstacles and pursue their goals. Whether it’s overcoming challenges or striving for self-improvement, this method offers a structured approach to introspection and problem-solving.
Setting and Achieving Goals
For striving to achieve milestones, the 5 Whys Technique provides a systematic way to examine potential barriers to success. By delving into the root causes of obstacles or setbacks, individuals can develop targeted strategies to overcome them and progress toward their desired outcomes.
How to Use 5 Whys Technique for Problem Solving?
The 5 Whys Technique serves as a powerful tool for problem-solving across various industries and scenarios. Let’s explore its application through two distinct case studies, shedding light on how this method can effectively uncover root causes and drive impactful solutions.
Case Study: Manufacturing Industry
Root cause analysis in a manufacturing setting is crucial as it can help with problem-solving and cost reduction processes. It’s proven to reduce costs by lowering downtime, minimizing defects, and enhancing overall processes. Here are a few use cases of the 5 Whys analysis in Manufacturing:
Identifying Production Bottlenecks
In the manufacturing sector, operational efficiency is paramount for meeting production targets and delivering high-quality goods. When faced with bottlenecks or slowdowns in the production line, the 5 Whys Technique can be employed to delve into the underlying causes. By repeatedly asking “why,” teams can identify the specific factors contributing to these bottlenecks, whether it’s machinery malfunctions, supply chain disruptions, or workforce constraints. This structured approach enables a comprehensive understanding of the issues at hand, paving the way for targeted interventions to alleviate production constraints.
Implementing Effective Solutions
Once the root causes of production bottlenecks are unearthed through the 5 Whys Technique, organizations can proceed to implement effective solutions. Whether it involves recalibrating machinery, optimizing inventory management processes, or enhancing workforce training, addressing these underlying issues directly contributes to improved operational performance. The systematic nature of this problem-solving method ensures that solutions are not merely superficial but are tailored to address fundamental challenges within the manufacturing environment.
Case Study: Business Problems
Achieving Business Goals and KPIs
In a business context, achieving strategic objectives and key performance indicators (KPIs) is essential for sustained growth and success. The 5 Whys Technique can be instrumental in dissecting barriers that hinder goal attainment. By iteratively questioning why certain business goals are not being met or why specific metrics are falling short, organizations gain insights into systemic issues affecting their performance. This methodical inquiry lays the groundwork for devising targeted strategies aimed at overcoming obstacles and driving progress towards desired outcomes.
Managing Time More Efficiently
Time management is a common challenge faced by businesses across diverse sectors. Through the 5 Whys Technique, organizations can unravel the underlying reasons behind time inefficiencies. Whether it pertains to prolonged project timelines, recurring delays in deliverables, or ineffective resource allocation, this method offers a structured approach to identifying core issues impacting time management practices within an organization. Subsequently, informed decisions and process improvements can be implemented to optimize time utilization and enhance overall productivity.
Tips for Mastering the 5 Whys Technique
Asking the Right Questions
Crafting Effective Whys
When utilizing the 5 Whys Technique, it is crucial to craft effective “why” questions. Each “why” should be carefully formulated to delve deeper into the underlying causes of a problem. By asking precise and targeted “why” questions, individuals and teams can uncover more comprehensive insights and avoid pitfalls, leading them closer to identifying the root cause. Crafting effective “whys” involves framing questions that are specific, open-ended, and focused on unraveling layers of causation.
Avoiding Assumptions
In the pursuit of mastering the 5 Whys Technique, it’s essential to avoid making assumptions when formulating each successive “why.” Assumptions can lead to biased conclusions and hinder the thorough exploration of underlying issues. Instead, maintaining an objective mindset and relying on factual evidence or observations ensures that each “why” question contributes to a genuine understanding of the problem at hand.
Documenting and Analyzing Answers
Keeping a Record
Documenting the answers obtained through the 5 Whys Technique is paramount for thorough analysis and future reference. By maintaining a record of each response elicited during the iterative questioning process, individuals and teams can track their investigative journey. This documentation serves as a valuable resource for retrospective analysis, enabling stakeholders to revisit past problem-solving endeavors and derive additional insights from previous investigations.
Identifying Patterns
Analyzing the documented responses allows for the identification of recurring patterns or common themes across different problem scenarios. Recognizing these patterns provides valuable clues about systemic issues or persistent challenges within an organization or personal context. By discerning patterns in the root causes uncovered through repeated application of the 5 Whys Technique, individuals can develop proactive strategies to address overarching issues comprehensively.
———————
I hope you found this guide to when and where to Use 5 why technique insightful and actionable! Stay tuned for more thought-provoking articles as we continue to share our knowledge. Success is rooted in a thorough understanding and consistent application, and we hope this article was a step in unlocking the full potential of Root Cause Analysis for your organization.
Reliability runs initiatives such as an online learning center focused on the proprietary PROACT® RCA methodology and EasyRCA.com software. For additional resources, visit EasyRCA Resources.
Ignite your curiosity, subscribe now!
Stay informed and connected with the latest updates by subscribing today!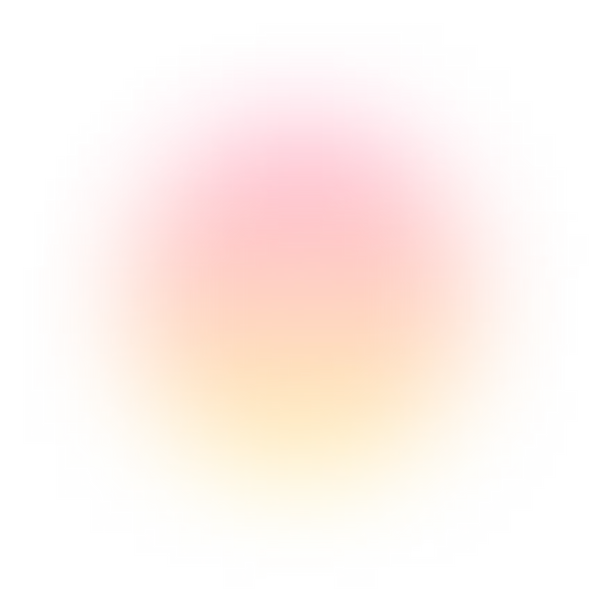
Recent Comments